Hi all,
Firstly I apologize if this has been posted before, but I am looking for a comparison between R&P and LS on the basis of linearly produced force. I find it difficult to get the right answers since most posts refer to these system being used in CNC machines for positioning.
I am working on a project that requires a linear force of 800N. Travel distance of 130mm, desired speed 30mm/s. When using the following equations for each device, I get the torque required for such an output.
R&P:
T=F.r
F=800N
r=0.004
T = 3.2N.m
Ball screw:
T=F.L(lead)/(2.pi.0.9)
F=800N
L=8
T=1.13N.M
I used a diameter of 8mm and a lead of 8 to ensure the same travel distance per revolution. From this is it safe to say that a ball screw would be the best solution since it requires less torque from the motor? Does the mass moment of inertia of the screw equate to a considerable increase in torque required, that should be accounted for?
This is only a rough estimate to decide which of the two would work best for the application.
Your input would be appreciated.
Thank you.
Rack & Pinion versus Lead/ball Screw
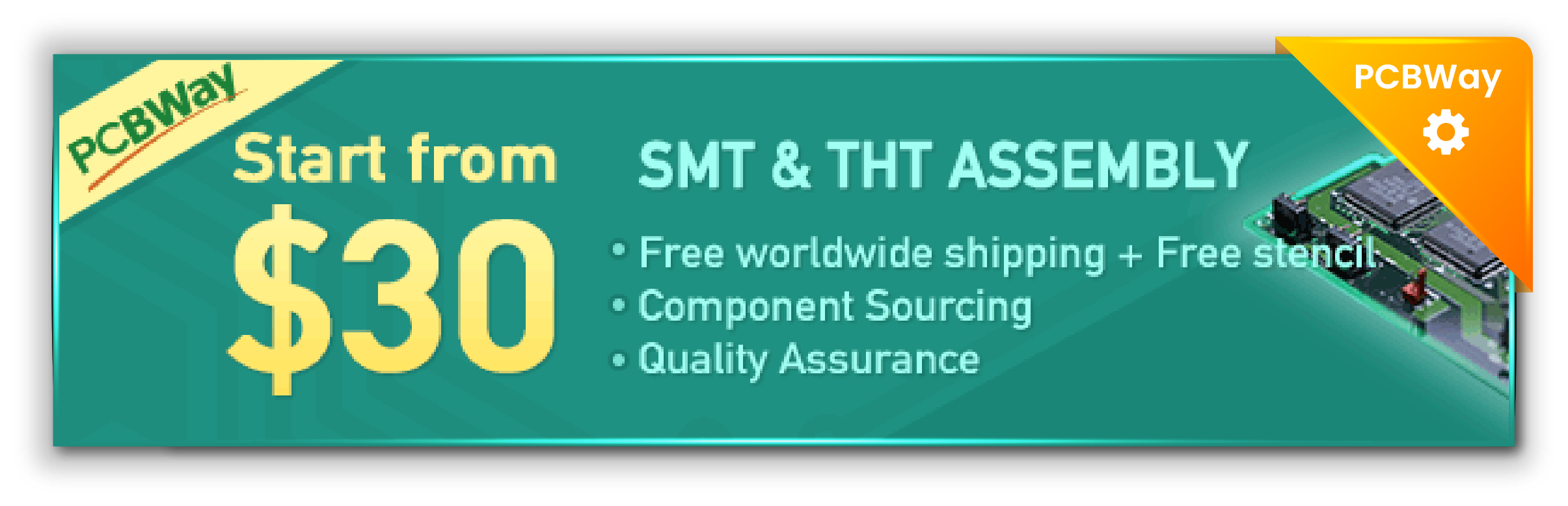