Design of a Load Cell
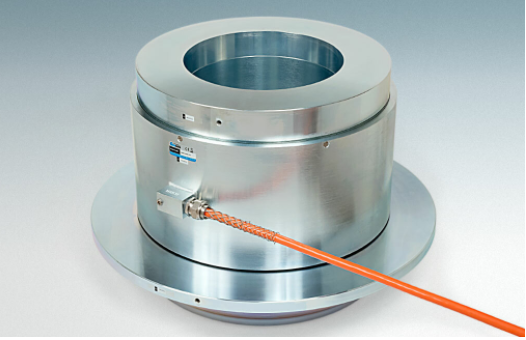
Hi Friends! Hope you’re well today. I welcome you on board. In this post today, I’ll walk you through the details on the design of a load cell.
Strain gauge load cells are widely used in various applications. They work on the principle of varying electrical resistance with elastic deformation in the conductor. The strain gauge comprises thin wires which are affected by a change in environment. Expansion or contraction in a strain gauge occurs with varying temperatures which results in creating noise and lack of accuracy in measurement. The life of the device may also be affected due to corrosion that may occur in the elastic element. In addition to the possible deterioration, the load cell itself may cause safety issues with regard to the environment.
For example, in a refinery or chemical industry, the ignition of flammable liquids or gases may occur due to the use of load cells. Therefore, they must be designed accordingly.
Hermetically Sealed
Hermetically sealed load cells provide the best protection to the environment. The load cell is sealed by welding, using epoxy or glass-to-metal bonding.
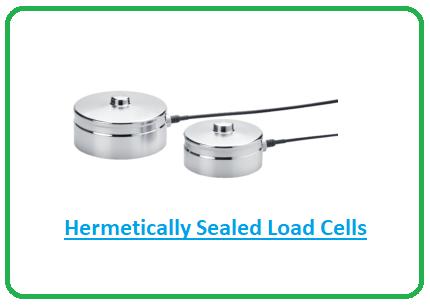
Pressurized inert gas is filled inside the cell. These load cells are standardized by Ingress Protection (IP) rating as air and watertight.
Open
These are designed in normal indoor conditions or special outdoor environments. Soft resin or rubber covering is used for environmental protection in this type of load cell.
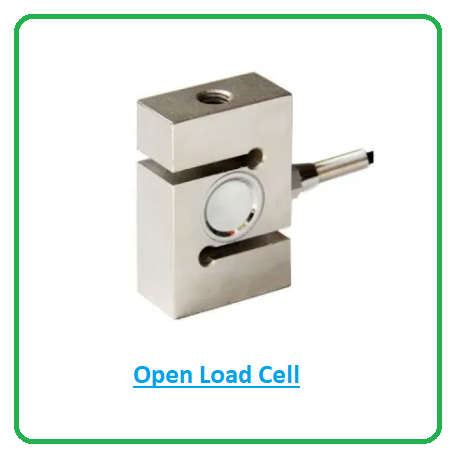
However, the strain gauge becomes vulnerable to moisture and change in temperature due to this type of protection.
Explosion-proof
As the name suggests, this type of load cell protects from any explosion that may occur within the device. If the internal cavities in a device or equipment are exposed to gases, these gases, once filled in the cavity, will lead to a potential explosion. An explosion-proof load cell is highly suitable for such conditions. Their rating is achieved by combining confinement, limitation of energy, and segregation.
Other factors to consider when designing a load cell are:
- The maximum weight that a load cell can measure is called Rated Capacity or rated load. Therefore, the load cell rated load must be greater than the weight to be measured in a system.
- Overload Rating (Safe) is the maximum load that can be exerted on a load cell without causing plastic deformation while measuring the weight of an element.
- Overload Rating (Ultimate) is the maximum load that can be exerted on the load cell without causing a fracture to the load cell.
- Rated Output is the ratio of the electric output signal and the strength of the excitation voltage expressed in mV/V.
- Zero Balance is the electric output signal with rated excitation voltage at no-load condition.
- Excitation Voltage is the voltage for excitation transferred to the circuit.
- Non-linearity defines the deviation of the calibration curve of the load cell from a straight line. It starts from zero loads up to the maximum capacity of the cell.
- Hysteresis is defined as the difference in the cycle a load cell follows while increasing the load from zero to maximum and then decreasing it from maximum to zero.
- Combined Error is calculated by measuring non-linear and hysteresis effects in combination.
- Repeatability is the measure of the difference between readings of repeated loads under the same loading conditions.
- Temperature Effect on Rated Output is the change in readings due to a change in temperature.
- Temperature Effect on Zero is the change in the zero-reading due to a change in temperature.
- Input and Output Resistance is the resistance of the circuit measured at the input and output respectively.
- Insulation Resistance is the measured resistance between the circuit and housing of the load cell.
That’s all for today. I hope you’ve enjoyed reading this article. If you have any questions, you can ask me in the section below. Thank you for reading the article.