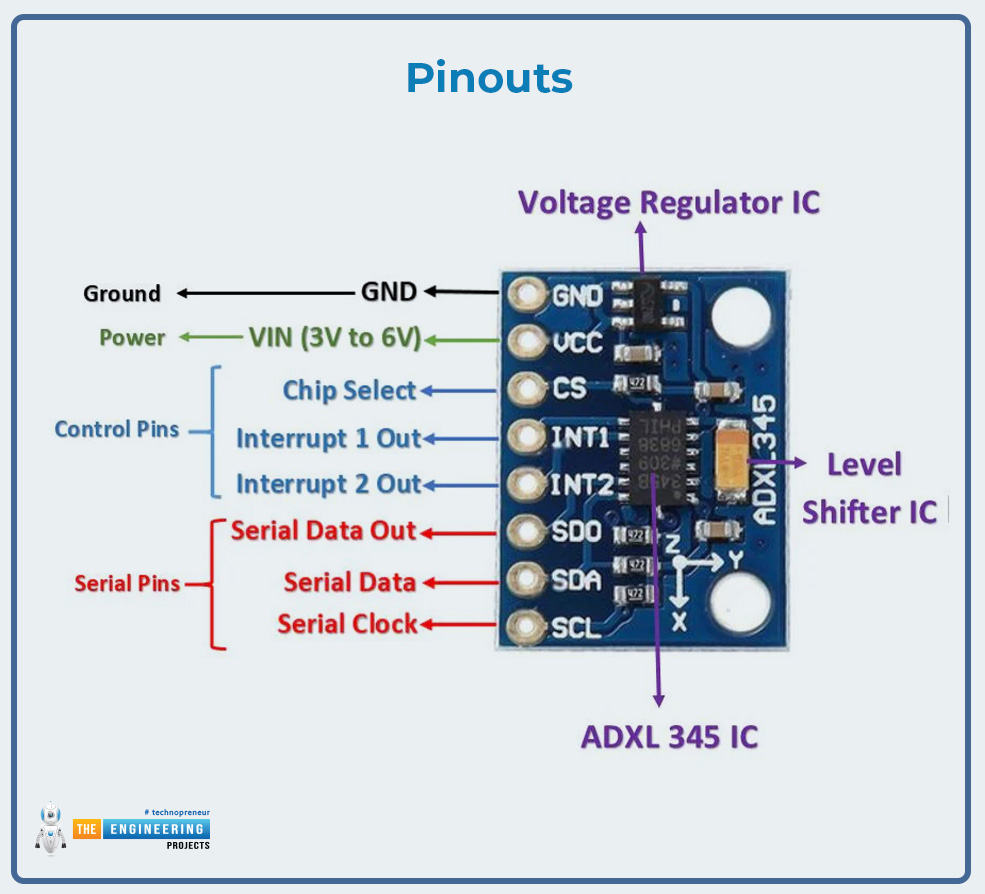
Hi readers! I hope you are fine and spending each day learning more about technology. Today, the subject of discussion is the ADXL345 3-Axis Digital Accelerometer. It may be something you were aware of or something new and unique.
The ADXL345 is a small form factor, high dynamic range, low power-consuming accelerometer designed by Analog Devices. It is used extensively in consumer electronics and is also applied in automotive systems to develop applications such as motion sensing and orientation detection, industrial automation, healthcare with applications such as vibration analysis, and so on.
This accelerometer offers range options of ±2g through to ±16g, up to 13-bit output resolution and integrated motion sensor samples that include tap, double tap, and free-fall. Due to its low energy consumption, it is suitable for portables and battery-operated appliances and can integrate I²C and SPI interfaces.
The ADXL345 detects the orientation, tilt, and motion when it is used to measure static and dynamic acceleration. It is applied in smartwatches, mobile phones, gamepads, and in medical instruments. The analysis of tasks like vibration analyzers and condition monitors can be supported in industrial sectors.
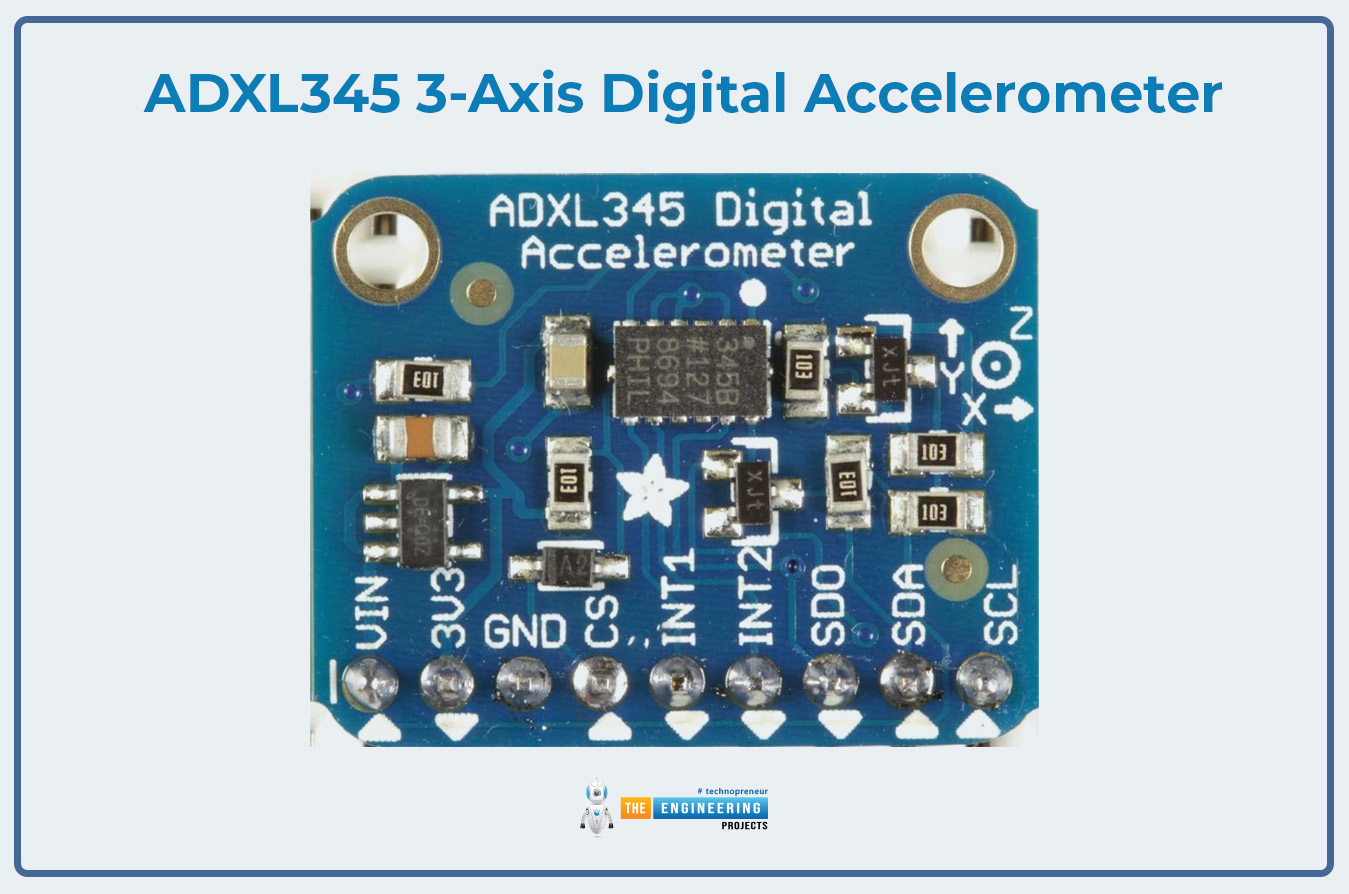
This book is a complete guide to the understanding of how the ADXL345 works, its functionality, and how it can be used. In a stable and highly flexible method, we can use the ADXL345 accelerometers to make the most of the optimum probability of creating the current and future designs that play crucial roles in improving the existing technology.
Introduction:
A small form and fast sensing accelerometer specifically developed by Analog Devices for use in motion sensing and orientation finding applications.
This device is low power and as such it can be utilized in battery-operated and portable apparatus.
Its usage is very large in home appliances, automobile electronics, industrial applications, and medical equipment.
Selectable measurement ranges from ±2g to ±16g, high-resolution output up to 13 bits, and embedded motion detection algorithms such as tap, double-tap, and free-fall detection.
Flexible communication interfaces such as I²C and SPI for easy integration into various systems.
Measures both static and dynamic acceleration for precise orientation, tilt, and vibration analysis.
Used in devices like mobile phones, wearables, game controllers, medical monitoring devices, and industrial vibration monitoring.
It enables the designers to come up with creative solutions, efficient, and reliable for modern technology.
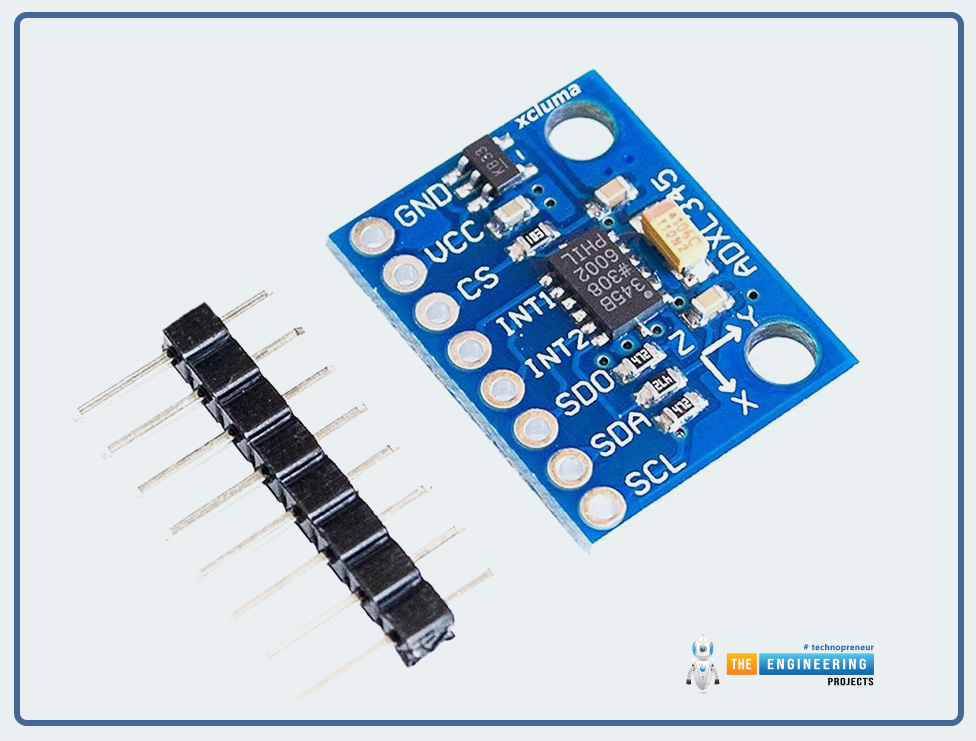
Datasheet:
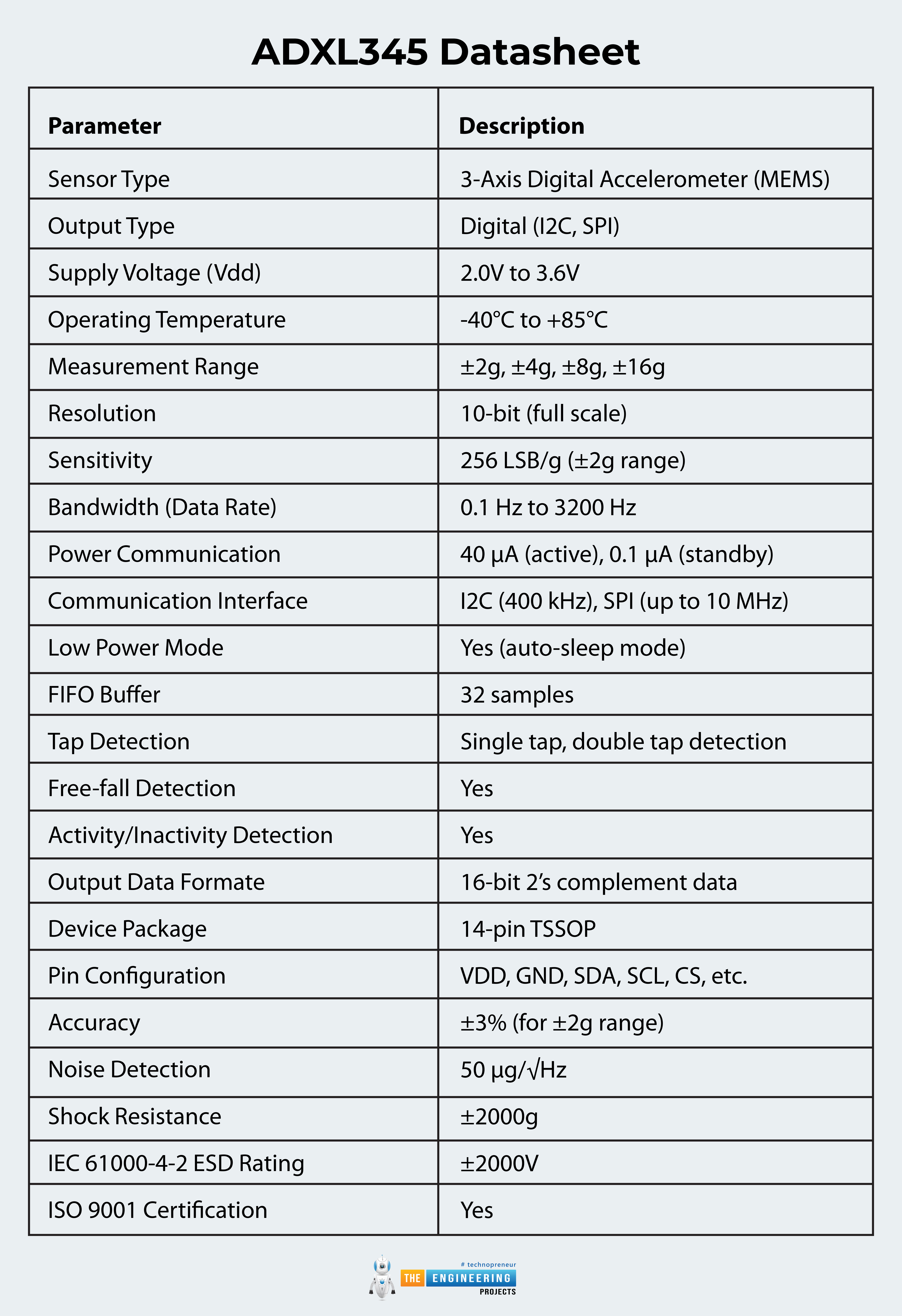
Parameter |
Description |
Sensor Type |
3-Axis Digital Accelerometer (MEMS) |
Output Type |
Digital (I2C, SPI) |
Supply Voltage (Vdd) |
2.0V to 3.6V |
Operating Temperature |
-40°C to +85°C |
Measurement Range |
±2g, ±4g, ±8g, ±16g |
Resolution |
10-bit (full scale) |
Sensitivity |
256 LSB/g (±2g range) |
Bandwidth (Data Rate) |
0.1 Hz to 3200 Hz |
Power Communication |
40 µA (active), 0.1 µA (standby) |
Communication Interface |
I2C (400 kHz), SPI (up to 10 MHz) |
Low Power Mode |
Yes (auto-sleep mode) |
FIFO Buffer |
32 samples |
Tap Detection |
Single tap, double tap detection |
Free-fall Detection |
Yes |
Activity/Inactivity Detection |
Yes |
Output Data Formate |
16-bit 2’s complement data |
Device Package |
14-pin TSSOP |
Pin Configuration |
VDD, GND, SDA, SCL, CS, etc. |
Accuracy |
±3% (for ±2g range) |
Noise Detection |
50 µg/√Hz |
Shock Resistance |
±2000g |
IEC 61000-4-2 ESD Rating |
±2000V |
ISO 9001 Certification |
Yes |
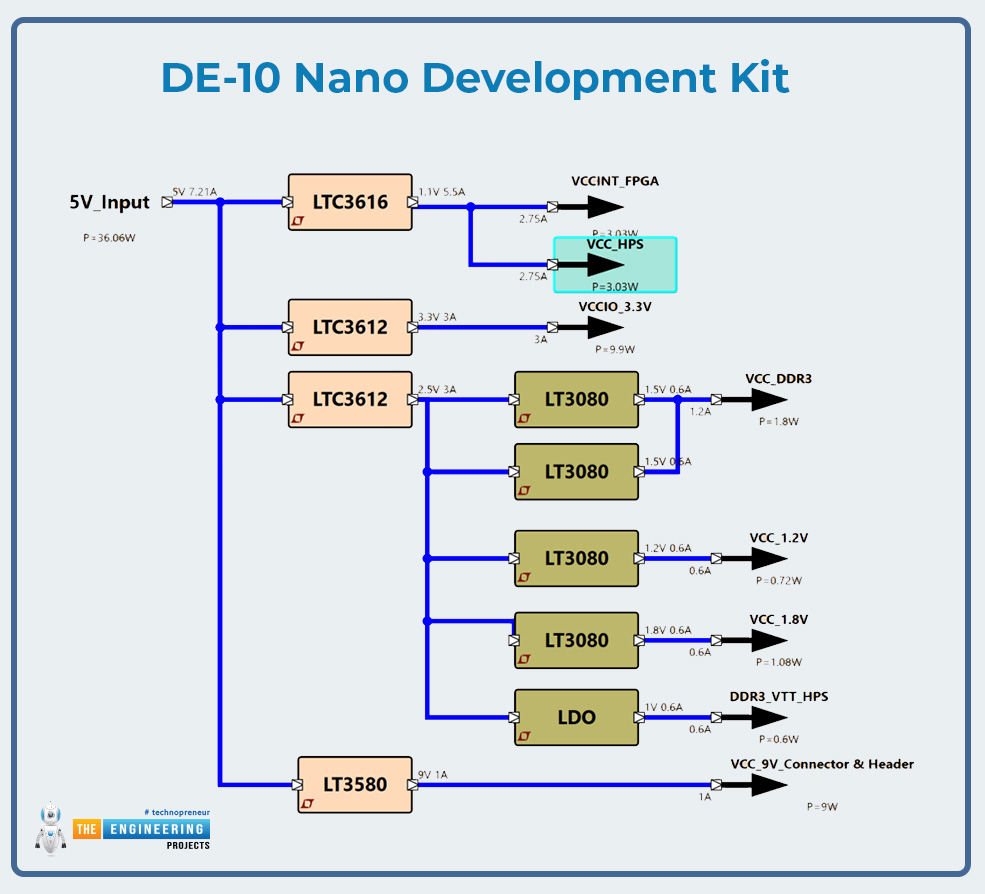
Pinouts:
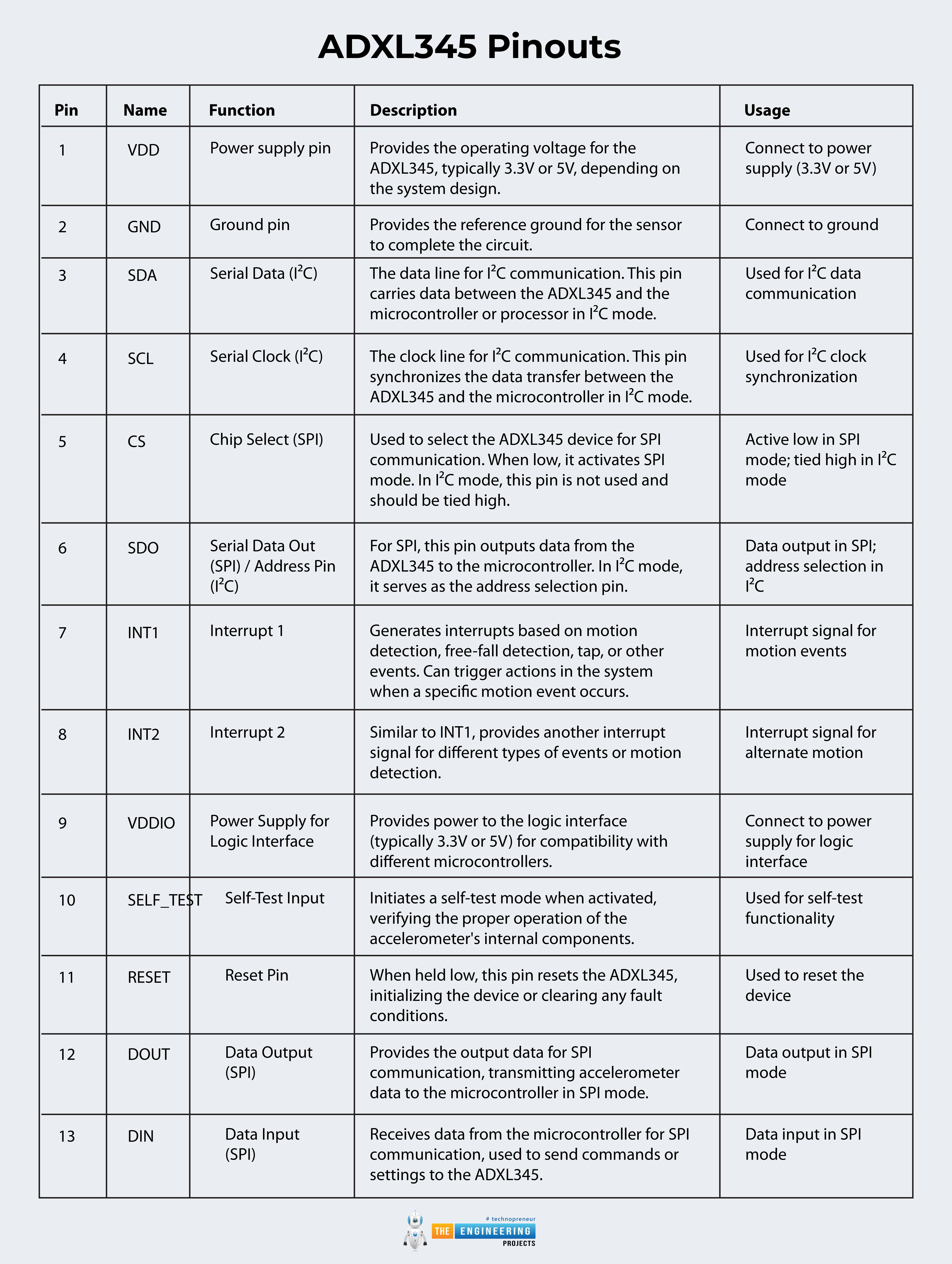
Pin |
Name |
Function |
Description |
Usage |
1 |
VDD |
Power supply pin |
Provides the operating voltage for the ADXL345, typically 3.3V or 5V, depending on the system design. |
Connect to power supply (3.3V or 5V) |
2 |
GND |
Ground pin |
Provides the reference ground for the sensor to complete the circuit. |
Connect to ground |
3 |
SDA |
Serial Data (I²C) |
The data line for I²C communication. This pin carries data between the ADXL345 and the microcontroller or processor in I²C mode. |
Used for I²C data communication |
4 |
SCL |
Serial Clock (I²C) |
The clock line for I²C communication. This pin synchronizes the data transfer between the ADXL345 and the microcontroller in I²C mode. |
Used for I²C clock synchronization |
5 |
CS |
Chip Select (SPI) |
Used to select the ADXL345 device for SPI communication. When low, it activates SPI mode. In I²C mode, this pin is not used and should be tied high. |
Active low in SPI mode; tied high in I²C mode |
6 |
SDO |
Serial Data Out (SPI) / Address Pin (I²C) |
For SPI, this pin outputs data from the ADXL345 to the microcontroller. In I²C mode, it serves as the address selection pin. |
Data output in SPI; address selection in I²C |
7 |
INT1 |
Interrupt 1 |
Generates interrupts based on motion detection, free-fall detection, tap, or other events. Can trigger actions in the system when a specific motion event occurs. |
Interrupt signal for motion events |
8 |
INT2 |
Interrupt 2 |
Similar to INT1, provides another interrupt signal for different types of events or motion detection. |
Interrupt signal for alternate motion |
9 |
VDDIO |
Power Supply for Logic Interface |
Provides power to the logic interface (typically 3.3V or 5V) for compatibility with different microcontrollers. |
Connect to power supply for logic interface |
10 |
SELF_TEST |
Self-Test Input |
Initiates a self-test mode when activated, verifying the proper operation of the accelerometer's internal components. |
Used for self-test functionality |
11 |
RESET |
Reset Pin |
When held low, this pin resets the ADXL345, initializing the device or clearing any fault conditions. |
Used to reset the device |
12 |
DOUT |
Data Output (SPI) |
Provides the output data for SPI communication, transmitting accelerometer data to the microcontroller in SPI mode. |
Data output in SPI mode |
13 |
DIN |
Data Input (SPI) |
Receives data from the microcontroller for SPI communication, used to send commands or settings to the ADXL345. |
Data input in SPI mode |
Features:
High Measurement Range and Resolution:
The ADXL345 offers programmable measurement ranges of ±2g, ±4g, ±8g, and ±16g, which allows it to meet a wide range of applications:
±2g and ±4g: Best suited for applications involving tilt sensing, low-impact motion detection, and orientation tracking.
±8g and ±16g: Best suited for high-impact applications such as free-fall detection, collision analysis, and high-acceleration monitoring.
With a resolution of 13 bits and sensitivity as low as 4 mg/LSB in the ±2g range, the sensor captures minute changes in acceleration with exceptional accuracy.
Resolution and Accuracy:
The ADXL345 has a 13-bit resolution with a sensitivity of 4 mg/LSB in the range of ±2g. This high resolution ensures that this sensor can detect even the minutest movements with excellent accuracy. It provides accurate measurement with a resolution down to 0.004g. High resolution and low noise make the ADXL345 capable of very subtle changes in movement that make it ideal for use in applications requiring precise orientation and motion sensing.
Flexible Data Output Rates:
The ADXL345 also boasts a flexible Output Data Rate capable of ranging from 0.1Hz to 3200Hz. This makes the sensor flexible for its usage in applications that use it for low-frequency sensing like tilting and orientation sensing and high-frequency sensing, like vibration analysis and real-time motion analysis. Users can make variations to the ODR following the particular requirements of the application to strike a balance between the amount of power being used and the levels of reactivity.
Communication Interface Options:
Communication interfaces enable the choice of which sort of communication is used, and there are several alternatives.
The ADXL345 offers two standard communication interfaces for data transmission: I2C and SPI. This makes their applicability likely over many microcontrollers and embedded systems since they should be compatible with both controller interfaces. The features of the communication protocol options make it possible to integrate the technology into different devices and appliances.
I2C Interface:
The ADXL345 employs an I2C interface operable at the highest speeds to 400 kHz which gives an easy and quick two-wire connection. This makes it ideal for use in systems where the board area is at a premium and power dissipation demands are kept to the minimum.
SPI Interface:
It is also designed for SPI communication interface up to 10 MHz. SPI provides a much larger bandwidth and therefore is used for transmitting data when real-time communication is necessary.
Being designed with interfaces such as the I2C and SPI, the ADXL345 can be easily implemented in different consumer electronic applications as well as industrial control applications.
Wider Working Temperature range:
The ADXL345 has been developed with the ability to function uniformly in temperature variations, that is, (- 40°C to +85°C), which makes it flexible and usable across several industries and personal uses. Being applied to different areas such as outdoors, automotive, or other industrial conditions where temperature variations can greatly affect it, the ADXL345 is capable of providing reliable operation no matter the temperature variations that may occur.
Owing to its wide operating temperature range, it finds application in automotive industries, environmental monitoring devices, and robotics, where the sensors are often used under extreme and fluctuating environmental conditions.
FIFO Buffer for Data Storage:
ADXL345 has an onboard feature of a 32–sample FIFO which means the sensor can store the samples of the acceleration data received first. The FIFO buffer plays the role of relieving the load of the host processor and also provides the sensor with a place to temporarily store data that awaits to be processed or transmitted. This feature enhances the function of the system by reducing the frequency of polling the sensor significantly.
In applications such as vibration analysis and moving object tracking, when a high amount of data is produced, the FIFO buffer can enhance the operating system performance and decrease the elapsed time.
Internal Sensors and Calibration:
Being an integrated circuit, the ADXL345 has its own internal sensors which are used to provide the three-axis acceleration values. These sensors are factory programmable, meaning that the sensor sports incredibly high accuracy as soon as it is manufactured. Moreover, users can fine-tune the sensor in the field if necessary, therefore increasing the level of accuracy in sensitive tasks.
The factory calibration makes the sensor output stable and accurate, reduces the effect of sensor drift, and improves the long-term stability of the sensor.
Compact and Lightweight Design:
The key feature of ADXL345 is its small size; it is combined in a single package measuring only 3 mm x 5 mm x 1 mm. This kind of portability makes it highly usable in devices that have limited space, for example, wearable technology, medical appliances, and IoT devices. Even though the size of the described sensor is relatively small it still offers acceptable performance and precision which could suit portable applications based on reduced weight.
Robustness and Durability:
The ADXL345 is, therefore, specially built to meet environmental stresses such as mechanical shock and vibrations. It can take up to 2000 g shock and therefore is quite useful for applications that require high-impact measurement such as catastrophic crash sensing and vibrating structures in industries. Another aspect I found promising is the longevity of the sensor, so if one is looking to run a sensor in a ‘rough’ environment, this will endure when other sensors have gone ‘belt and braces’.
Working Principle:
MEMS Sensor:
The MEMS accelerometers in the ADXL345 are made of a micro-machined silicon structure arranged on a spring mechanism. This structure shall offer a chance to move with acceleration forces. The MEMS technology employs capacitive sensing elements that are capable of sensing the motion of the structure in the X, Y, and Z directions.
When signal acceleration is detected by the ADXL345, then the silicon mass inside the sensor displaces along the particular axis of motion and this displacement, in turn, introduces a change between the electrodes and the mass capacitance. Capacitance change is directly proportional to the acceleration, that has been applied. This capacitance change is converted into analog to digital form which is the output of the accelerometer.
Capacitive Sensing Mechanism:
Capacitive sensing is the main technique by which ADXL345 measures the acceleration that occurs in the device. The MEMS device announced here comprises many steady electrodes and only one suspended mass. Whenever the accelerometer undergoes any change in the velocity along the x, y, or z axis, the mass displaces, and this results in a change in the distance between the electrodes. This in turn causes a shift in the capacitance of the fixed electrodes to the moving mass capacitance.
The ADXL345 has two pairs of capacitors per axis: A single batch of capacitors is employed to amplify the acceleration along a positive axis, for instance, the X+, and another batch for the negative axis, X-. The difference in capacitance between the two pairs will enable the sensor to determine the direction of the movement in pulling or pushing the object and determine the magnitude of the acceleration.
Signal Conditioning:
After the capacitive sensing elements are triggered by a change in acceleration, these small changes in capacitance are converted into an electrical signal that needs additional analysis. The ADXL345 contains an in-built signal conditioning circuitry that filters and amplifies the raw signal. This circuit is beneficial in guaranteeing a linear and more stable sensory output signal.
The analog signal output is then converted to a digital signal by incorporating an analog-to-digital converter (ADC) present in the ADXL345. As is seen in the design, the digital signal output is in the form of a binary code that corresponds to the acceleration measured in X, Y, and Z directions. The digital signal is consequently scanned, amplified, and regulated depending on the established measurement range.
Measurement Range and Sensitivity:
Measurement Range and Sensitivity is a commonly found section in instrument specifications that enables the determination of the area where the instrument can operate and how well an instrument performs its intended function at a given operational level.
Adjustable measurement ranges of the ADXL345 are ±2g, ±4g, ±8g and ±16g to suit different applications. The measurement range means how high an acceleration the sensor can measure and is set using the device’s registers through software.
Increased sensitivity is measured at lesser ranges, such as ±2g, while the reduced sensitivity is applied to larger ranges like ±16g.
The output from the accelerometer is given in the form of an analog top graph representing acceleration force (in g), where 1 g =9.81m/s2 (acceleration due to gravity). The digital output is in 2’s complement 16-bit format and further processing of the acquired raw data provides the user with acceleration in units of g.
The ADXL345 is designed to measure static and dynamic b accelerations as well as accelerations due to gravity. The ranges of accelerations in terms of G and resolution allow ADXL345 to be used for applications from basic tilt measurements to applications that require high-impact detection.
Applications:
Consumer Electronics:
Smartphones/Tablets: Used for screen orientation, gaming controls, and gesture recognition.
Wearables: Powers activity tracking, fall detection, and sleep monitoring.
Automotive Systems
Vehicle Stability Control: Measures lateral acceleration for safety systems like anti-rollover.
Crash Detection: Monitors high-impact events for black boxes and airbag deployment systems.
Industrial Automation:
Vibration Monitoring: Identifies machine health issues through vibration patterns.
Robotics: Tracks motion for joint control and navigation.
Healthcare:
Prosthetics and Orthotics: Measures patient movement for adaptive response systems.
Medical Devices: Monitors physical activity and falls in elderly care.
Gaming and AR/VR:
Motion Controllers: Capture hand movements to create a more immersive game experience.
Head-Mounted Displays: Track head orientation for virtual reality applications.
Conclusion:
The ADXL345 3-axis digital accelerometer is a versatile and powerful tool for modern motion sensing applications. Its high accuracy, low power consumption, and advanced features make it indispensable for a wide range of industries. From consumer devices and automotive systems to industrial machinery and healthcare, the ADXL345 empowers engineers to design smarter, more efficient products.
As technology advances, the ADXL345 remains a cornerstone in motion detection and orientation sensing, driving innovation in wearable tech, robotics, gaming, and beyond. Its adaptability, precision, and ease of integration ensure it remains a vital component in the ever-growing field of smart sensing solutions.