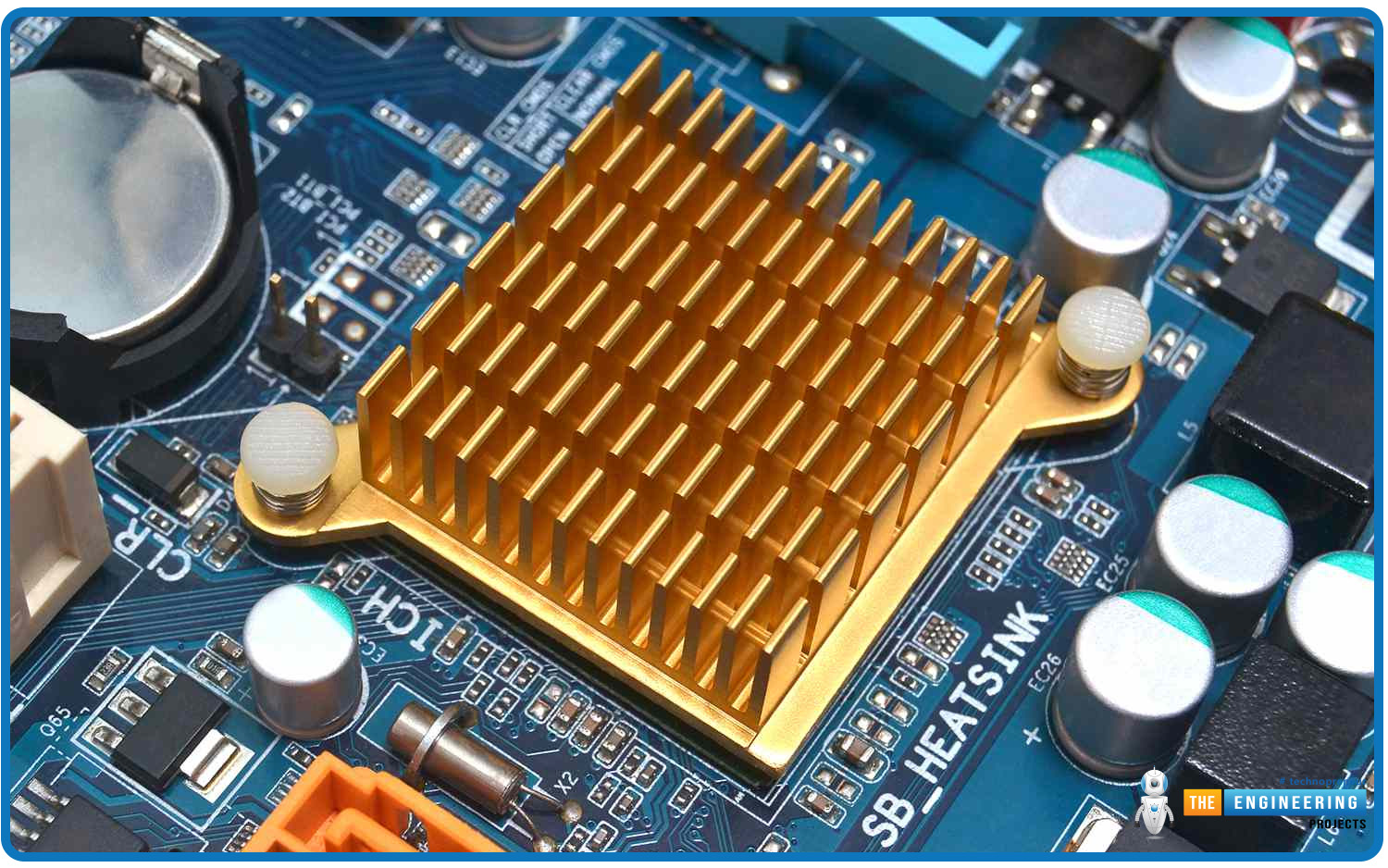
Heat sinks are the electric routes for heat elimination from the PCB body. The digital electronic world is all about making devices compact and more powerful. This is possible only when the printed circuit boards (PCBs) are small enough to fit into the compact device. The increasing demand for power in low space comes with different challenges, of which the most crucial is the heat management of PCBs. The heat sinks are made of elements such as copper, aluminum, diamond, ceramic materials, graphite, etc., and play a crucial role in the thermal optimization of PCBs for optimal performance and long life. This comprehensive guide is about the basic introduction, heat transfer methods, key parameters, design considerations, and manufacturing techniques involved in the heat sink from the PCB point of view.
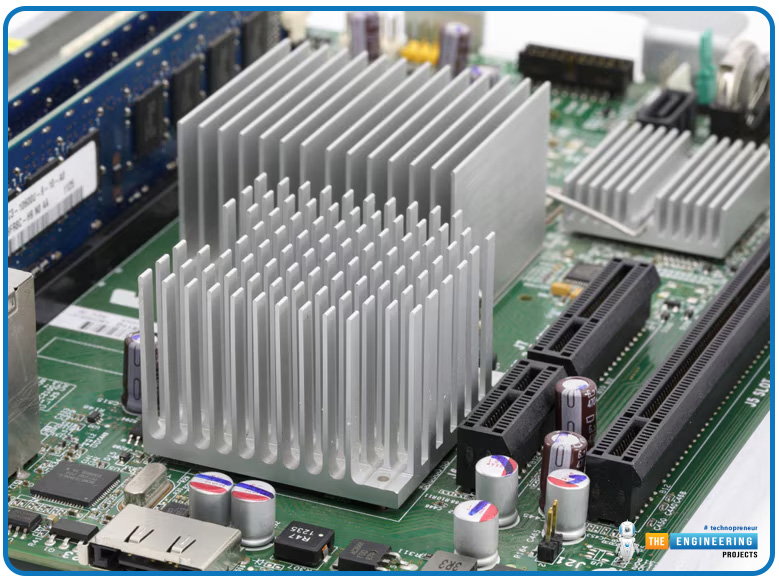
Where to Get Thermally Optimized PCBs?
PCBWay is the leading PCB manufacturer and has the honor of introducing the CRM management system to China and international companies for the first time. Before moving on to the theoretical information about PCB heatsinks, let’s discover the basic features of the platform master in providing all kinds of PCB manufacturing services, including high-heat performance PCBs. They provide all PCB-related services, including PCB prototyping, assembly, CNC, 3D printing, and much more. Customer satisfaction is their priority; therefore, they have made the process very smooth, whether it is the quotation procedure or the order tracking.
The good thing about PCBWay Fabrication House is the quick and easy services, special deals, and discounts with the same working quality. If you want to check the current deals or special discounts, you can check their web page:
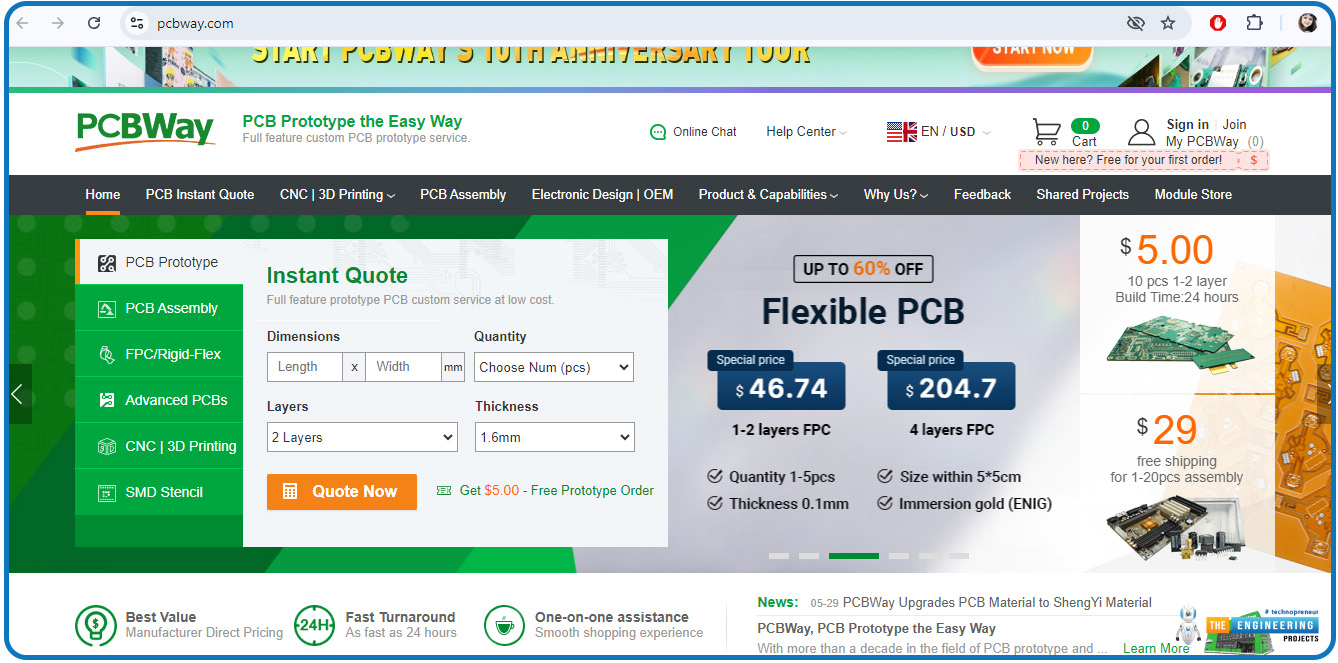
Even if the customers come with incomplete or ambiguous ideas about their projects, they can benefit from the PCBway services and book one-on-one assistance for their PCB-related queries. In short, this is the ultimate place to get all types of help, manufacturing, and work about the PCB, and a great number of positive reviews is proof of their smooth services and outstanding products.
Introduction to Heat Sinks
Heat sinks are the essential components in printed circuit boards that dissipate excess heat from the board and help with thermal management. The electronic components on the PCBs eliminate a lot of heat during their performance, based on the type of PCB and its duty time. Proper heat management is crucial for PCBs to ensure they work in safe temperature ranges and provides the best performance even when working for hours. The following are the basic parts of heat sinks:
Heat Sink Base Plate
It is made of high-conductive material to absorb more heat and eliminate it through the fins and also provide a solid foundation for the whole heat sink.
Heat Sink Fins
These are extended plates from the base plate, and the whole heat sink is identified through it. The common heat sink types are straight, louvered, and pin, and the density of the fins determines the thermal dissipation rate.
Thermal Interface Material (TIM)
It is a layer of a specific material placed between the heat sink and PCB to improve thermal contact.
Cooling Medium
The agency through which the heat is transferred to the external environment is called the cooling medium, and the most common examples are air or fluid.
Mounting Mechanism
This is the attachment method of heat sink to PCB and include the fastener or adhesives.
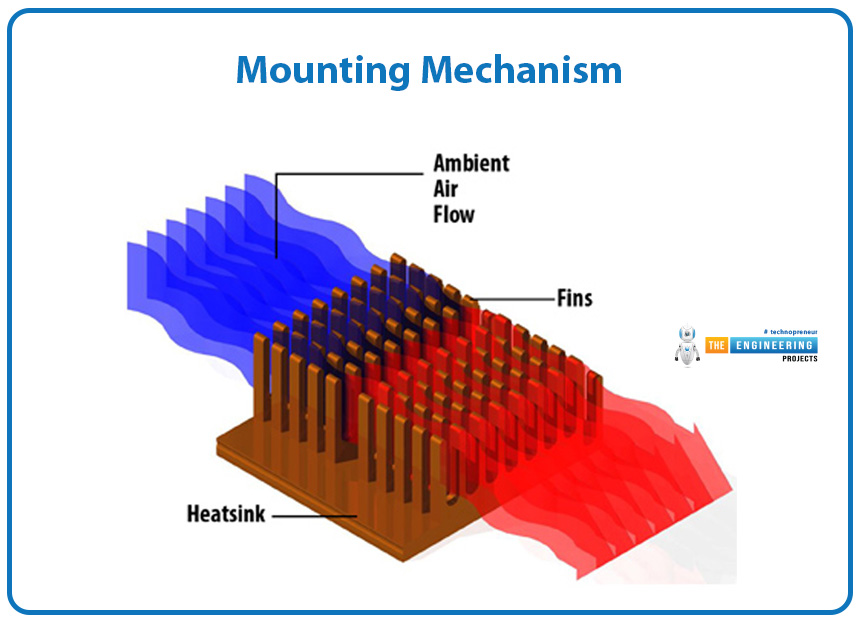
The smaller size and high demand for performance from the PCBs have made the manufacturers think more seriously about dissipating the excess heat, and this has enhanced the value of heat sinks. Heat sinks are engineered near the critical components to draw the heat away, disperse it into the surrounding environment, and prevent overheating for optimal performance.
Basic Heat Transfer in a PCB Heat Sink
It is essential to learn the core heat transfer objectives to understand the types, basic principles, and other related information about heat sinks. Heat transfer occurs through three basic phenomena, and let’s discuss each of them from the PCB point of view:
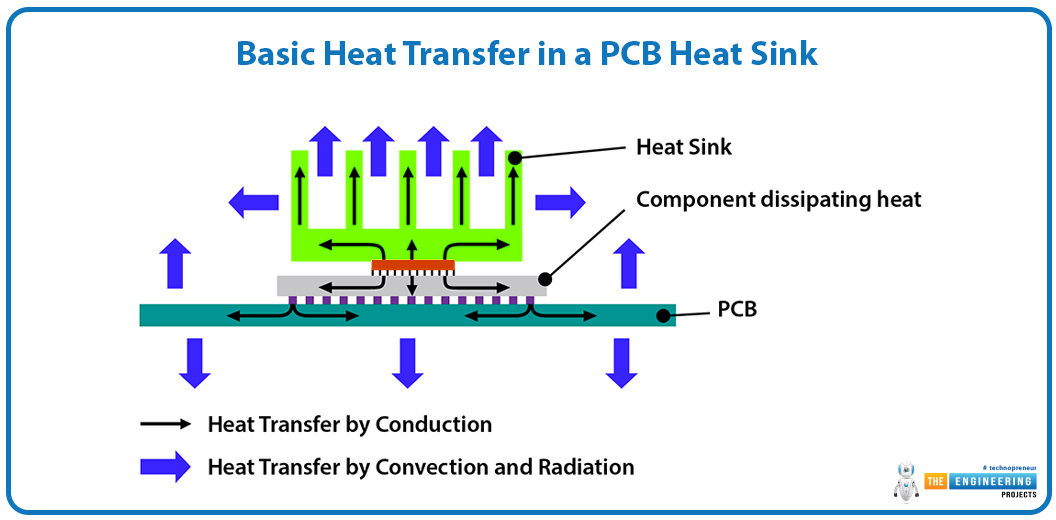
Conduction in PCBs
Conduction is the phenomenon of heat transfer from one object to another through direct contact because of the temperature difference between them. In PCBs, conduction occurs when the electrical components expel heat and it transfers toward the heat sink. The transfer rate and efficiency of the heat sink depend on the heat sink and PCB material. It is the most uncomplicated and common type of heat transfer.
The optimal place for the heat sink is exactly on the hotspots, and the most common ones are thermal spreaders, integrated circuits, resistors, etc. When the aim is to provide thermal conductivity through conduction, the manufacturer connects the heating component with the heat sink. Moreover, the fins are connected directly to the hotspot for direct heat elimination towards the external environment.
Convection in PCBs
Convection is the heat transfer from one object to another through fluid movement. In PCBs, convection occurs when the air passes through the heat sink, which eliminates the heat by cooling it down. Basically, there are two types of convection:
Natural Convection
Forced Convection
Natural convection occurs without the help of external equipment or power consumption. This process is comparatively slow, and when designing a heat sink for natural convection, these must be carefully oriented so the air can directly flow through the fins and help cool down the whole PCB system.
On the other hand, forced convection requires an external source, such as a power fan, that takes the power but expels all the heat at a higher rate.
Radiation Process in PCBs
Radiation is the process of heat transfer from one point to another through electromagnetic radiation. It is a good source of thermal optimization in PCBs but is a less common method as compared to conduction and convection. It is simply a phenomenon of heat elimination from an object on a PCB, and the rate of heat transfer depends on the material, surface area, and position of the component emitting heat.
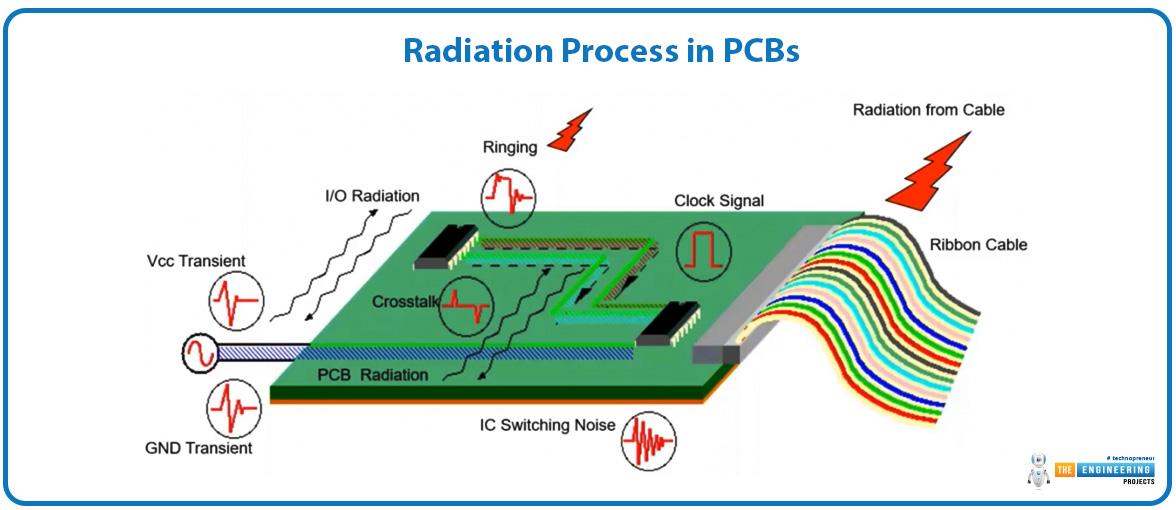
The frequent way to make the heat sink more efficient for radiation is to maximize the infrared wavelength. For this, the heatsinks are made of anodized aluminum to make them more efficient with radiation heat and thermal mechanisms. Moreover, the large surface area is another measure for the same purpose. This heat removal process is useful in heavy-duty and high-temperature applications, and the most supporting point about this method is that radiation is the only heat transfer method in vacuum applications.
Key Parameters in PCB Heat Sink Performance
When measuring the PCB heat sink performance and designing their locations, multiple factors are kept in mind, and here are some general parameters:
PCB Heat Sink Thermal Resistance (Rθ)
Thermal resistance is the critical point when designing the heatsink. It is the material’s ability to resist the heat flow from the body to the environment. Therefore, low heat sink thermal resistance shows better heat dissipation and is preferable. A higher conductivity of the material means lower thermal resistance. Other factors to judge the thermal resistance are the component's geometry, thermal interface material (TIM), mounting pressure, and the amount of air flowing through the heat sink.
PCB Heat Sink Thermal Conductivity (k)
It is the ability of the heatsink to conduct the heat, and the unit to measure it is the W/m·K (watts per meter-kelvin). Elements like copper and aluminum have high thermal conductivity and are considered better options for creating heat sinks. Similarly, plastic and other nonmetals have very low conductivity values.
At very high temperatures, the thermal conductivity of the material is affected, and this results in the unexpected behavior of the material. Moreover, the structure and geometry of the heatsink are another factor affecting the thermal conductivity.
PCB Heat Sink Fin Design
The fin design is another critical point to consider when measuring the heat sink performance of the PCB. The shape, size, position, and spacing influence the thermal management through the heat sink.
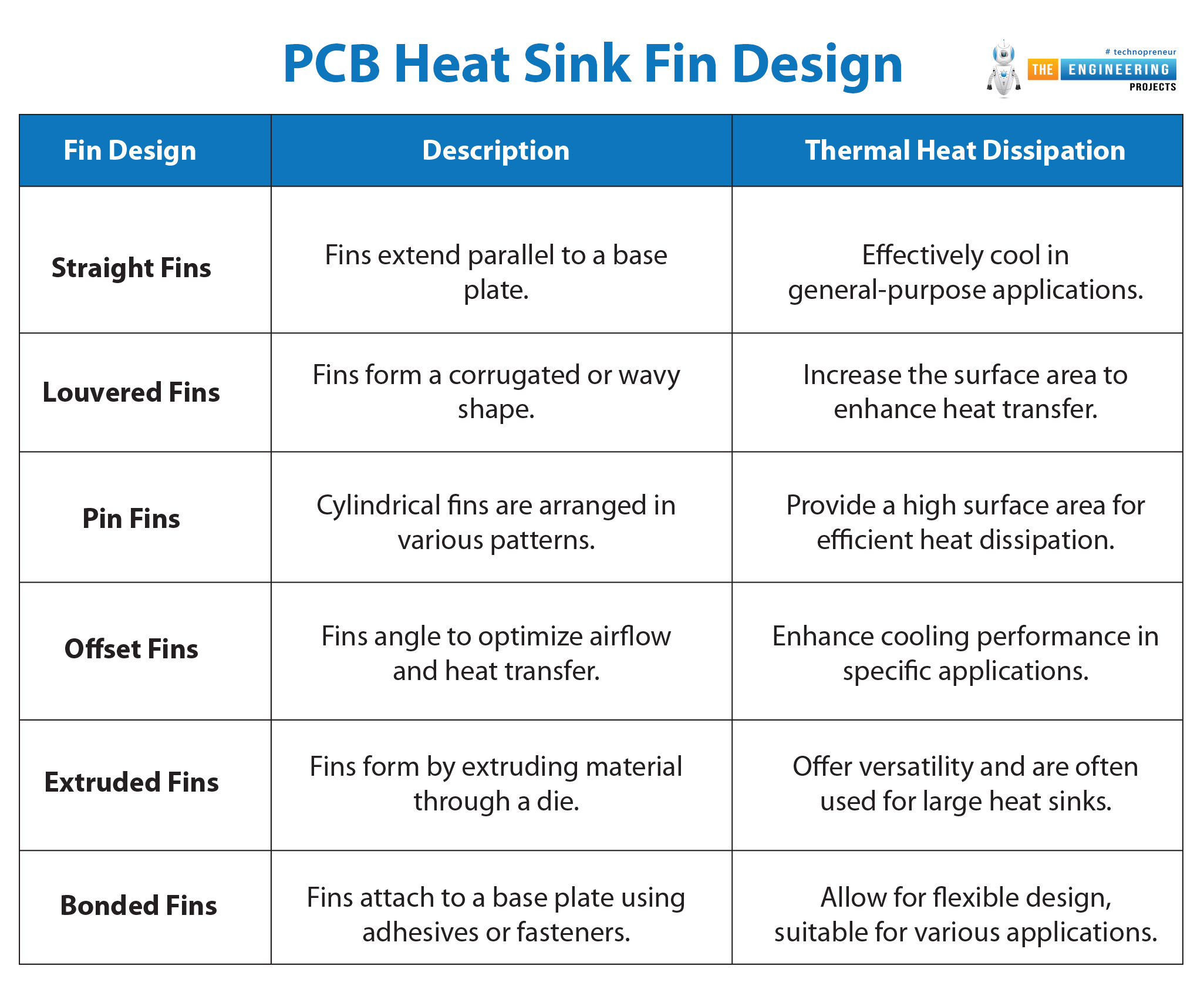
Fin Design |
Description |
Thermal Heat Dissipation |
Straight Fins |
Fins extend parallel to a base plate. |
Effectively cool in general-purpose applications. |
Louvered Fins |
Fins form a corrugated or wavy shape. |
Increase the surface area to enhance heat transfer. |
Pin Fins |
Cylindrical fins are arranged in various patterns. |
Provide a high surface area for efficient heat dissipation. |
Offset Fins |
Fins angle to optimize airflow and heat transfer. |
Enhance cooling performance in specific applications. |
Extruded Fins |
Fins form by extruding material through a die. |
Offer versatility and are often used for large heat sinks. |
Bonded Fins |
Fins attach to a base plate using adhesives or fasteners. |
Allow for flexible design, suitable for various applications. |
In addition to these, the heatsink surface area, position, and airflow are important factors to consider for the PCB heatsink performance.
PCB Heat Sink Design Considerations
Several considerations are adopted for the expected performance while designing the heatsinks for the right thermal optimization on PCBs. Here are some of these:
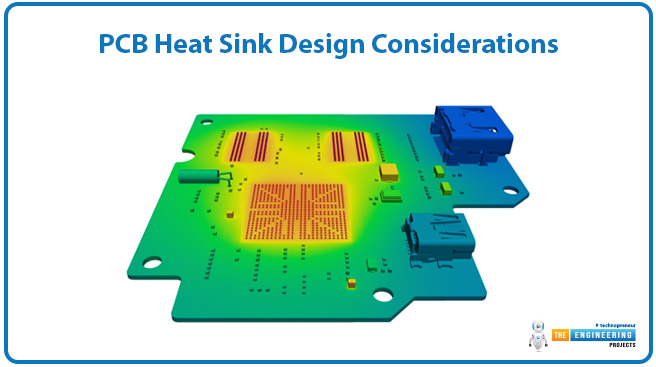
PCB Heat Sink Geometry
This is the most basic and obvious point that designers have to keep in mind while designing the heat sink for PCBs. Every design is different in surface area, size, and airflow; therefore, the manufacturers have multiple choices according to the PCB type. Some popular heat sink designs are cross-cut, straight fin, and pin fin, and the choice of a particular design depends on the heat dissipation requirements, available airflow, and total space for the heat sink formation.
PCB Heat Sink Thermal Interface Material (TIM)
These are the crucial gateways for the heat elimination of electronic components from the environment. They help to fill the gaps between the components and make the thermal optimization smooth. Some general TIMs are thermal grease and thermal pads, phase change materials (PCMs), thermal tapes, etc., and the right choice of TIM is the key to better heat elimination from PCBs. As a result, the thermal resistance decreases, and more heat dissipates into the surrounding area.
PCB Heatsink Attachment Methods
The main heat elimination methods for heat sinks are convection and conduction, and these depend on the perfect contact of the heat sink with the PCB surface. This connection is accomplished using different types of mechanical fasteners, and some common examples are:
Screws
Clamps
Press fit
Clip ons
Adhesive-based attachments
While choosing the right attachment method for a heat sink, always consider parameters such as mechanical stress, compatibility, ease of assembly, etc.
PCB Heatsink Manufacturing Methods
Now let’s discuss the fundamental techniques for crafting the heat sinks in the PCBs for the best thermal optimization.
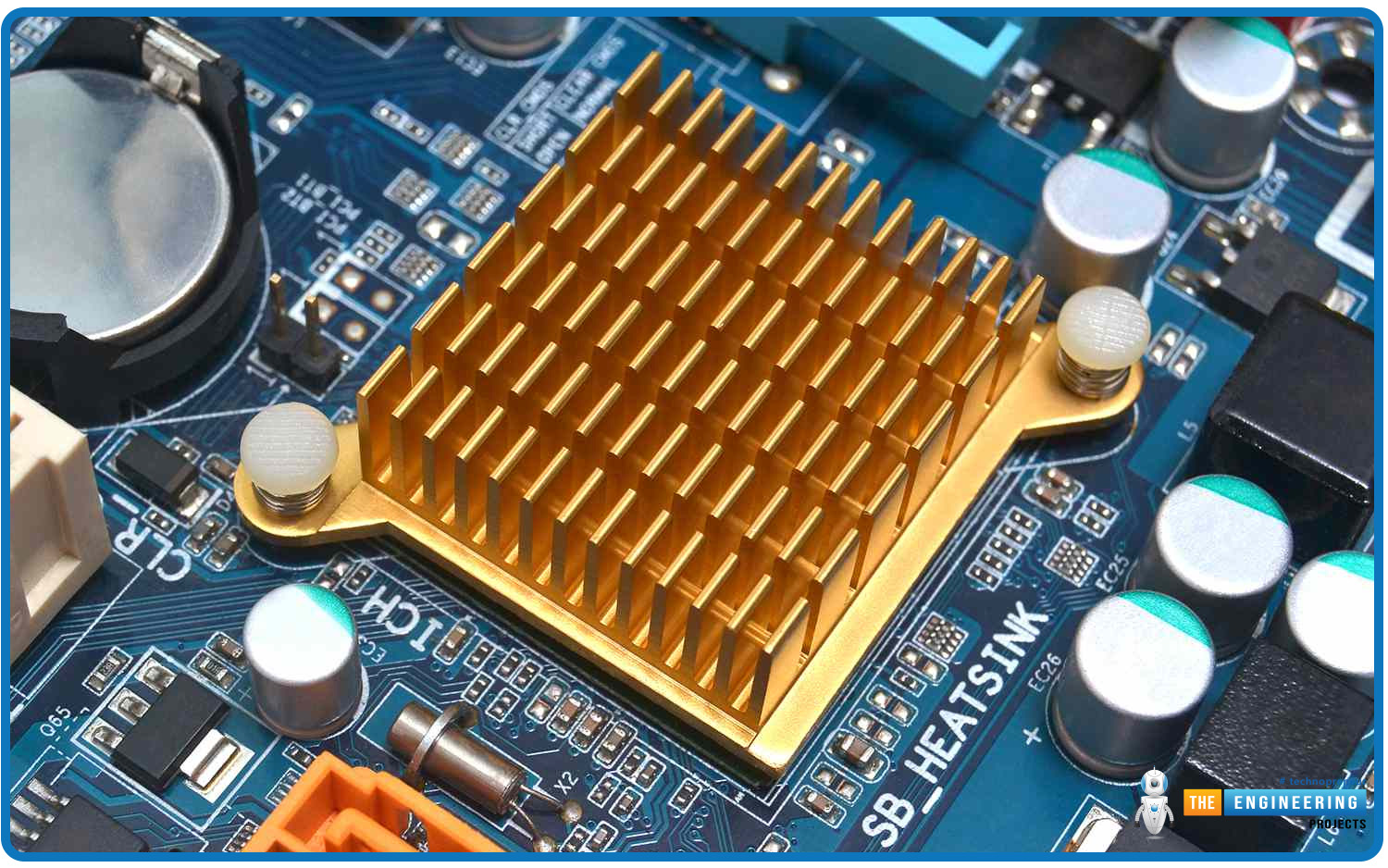
PCB Heat Sink Extrusion
This manufacturing technique is applied to create the customized heat sink for the PCBs. Here, the heat sink material is usually heated aluminum or copper that is forced through the die to create long-shaped heatsinks with a good cross-section area. The resultant material is then cut into the desired size. The pluses of this technique are precision, efficiency, consistency, and customization according to the manufacturer’s choice. It is usually preferred for LED lights, consumer electronics, and commonly used appliances.
PCB Heat Sink Die Casting
Die casting is the method in which the molten metal is injected into a mold under high pressure to shape the metal according to the PCB’s requirements. This is preferred where complex heat sink shapes are expected to create highly intricate designs and details. Moreover, this is a perfect option for high-volume production in less time.
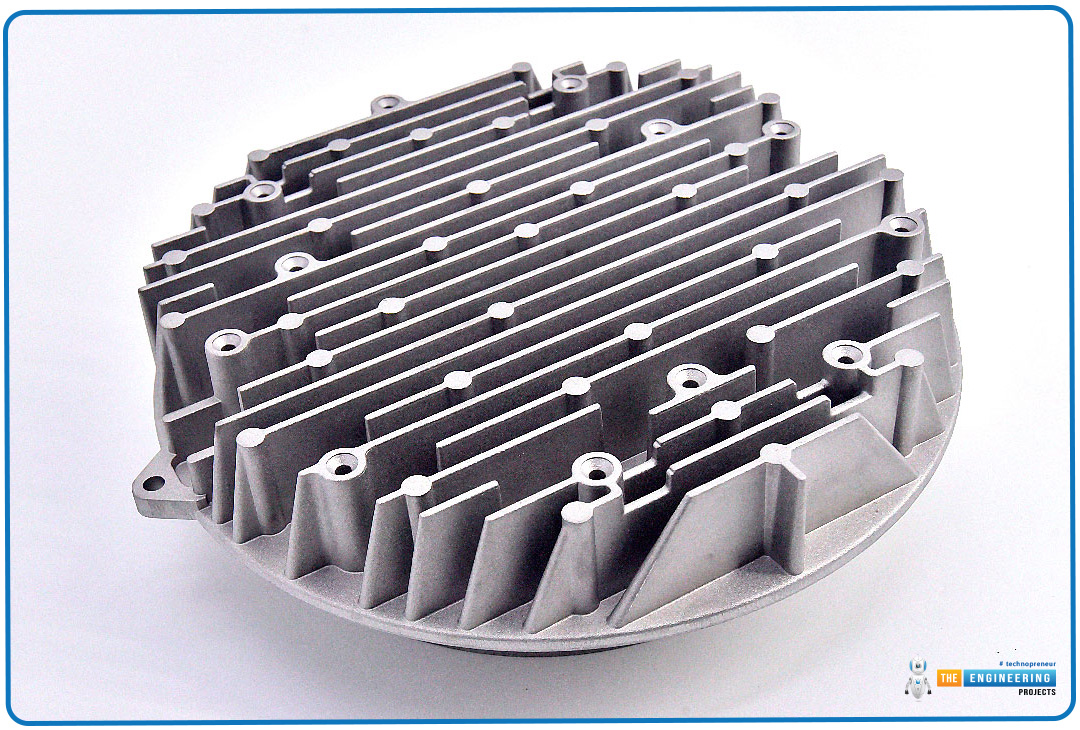
PCB Heat Sink Die Forging
It is a traditional way to get the right heat sink shape through the localized compressed force of a hammer or die, and the heat sink formed as a result has great mechanical strength. The parts made have high mechanical strength and thermal resistance. This technique is applied to create heat sinks for the PCB, which is expected to be utilized in high-performance fields such as aerospace or military.
PCB Heat Sink Skiving
This method involves the formation of a heat sink by cutting the flat metal sheets. The metal is sliced and bent according to the size, area, and shape of the heat sink required. It is a comparatively complicated method and is applied to create a high-density fin structure so that thermal dissipation occurs at a high rate. This method is applied to high-duty electronic components such as GPUs, CPUs, etc.
PCB Heat Sink Bonding
This is a relatively straightforward technique for heat sinks that involves fin attachment to the base through thermal adhesion or solder. The manufacturers have the independence to use different material types and customize them according to the PCB type and thermal requirements. The flexible design results in better performance and reliability.
Hence, this was your guide for the PCB heat sinks, and I hope you got all the information about the topic for what you were searching for. If you want more information, you can ask in the comment section.