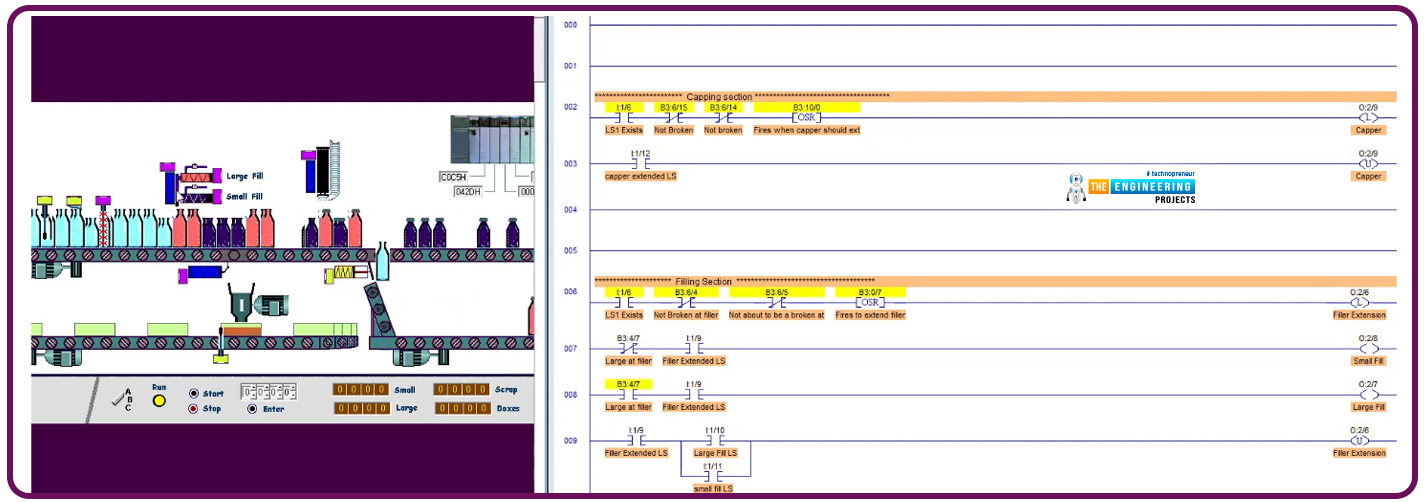
Hi, my friends, and welcome back to enjoying together learning and practicing PLC ladder logic programming with a new project from the actual industry. Today my friends, we will continue the bottle line project to complete the capping and filling of the bottling line. As usual, we will describe the requirements as the clients ask us to do. Then we list all the inputs and outputs we will use to make our design work. Afterward, we write the ladder logic program into two sub-tasks. We make one to perform the filling and the second for the capping process. So, without further delay, buddies, let’s jump into the work.
Filling and capping project
Let me introduce the project as two processes we have been requested to implement here. We are filling bottle process in which we need to control the filling station that has two supplying sources to fill the small bottles and the large-size bottles with two different liquids. Figure 1 shows the filling station that offers two sources of liquids: the orange-coloured liquid for the large-size bottles and the violet-coloured liquid to fill the small bottles. So we need to identify the type of bottle that comes to the filling station—then, based on knowing which bottle type, we need to open the valve of the appropriate filling tube. Remember to stop the main conveyor while the filing process is in progress. Once the filling has been done, we need to resume the movement of the main conveyor.
Moving on to the capping station, figure 2 shows the capping station that is nothing but a cylinder to let the cap released to the bottle that reaches the capping station. Now you can see my friends, inputs and outputs are listed and named on the filling and capping station. We need to list these inputs and outputs and see how we can employ them to complete our project. Please note, buddies, the recorded inputs and outputs in table 1 are not all project IOs. They are only the IOs belonging to the filling and capping process. So you can add these IOs to the list of IOs we have previously introduced in the last two tutorials.
Filling and capping stations IOs
Table 1 tabulates the list of IOs of the project, including names, addresses, and descriptions. As you can see, everyone, all information, including the item name, addresses, and description of the filling station, are in the table below and ready for your turn to use them in the logic of the program you will write.
Item name |
Address |
Description |
LS1 filling |
I:1/9 |
This level switch tells if the bottle is filled or not. |
Filling actuator solenoid SOL1 |
O:2/6 |
The filling valve actuator |
valve1 |
O:2/7 |
Purple liquid tube valve actuator |
Valve2 |
O:2/8 |
orange liquid tube valve actuator |
LS 2 |
I:1/10 |
Sensor to detect the filling position of the orange-coloured liquid for the large-size bottles |
LS 3 |
I:1/11 |
Sensor to detect the fill position of the purple for the small size position |
Similarly, table 2 lists the inputs and outputs that could be used throughout your program to achieve the requirements that your client has requested. Now, folks, our clock says the time to design and code the ladder logic program of the capping and filling system. so let’s go nailing the two processes.
IO name |
Address |
Description |
LS3 |
I:1/12 |
The position sensor of the cylinder actuator of the capping station |
Capping Actuator solenoid SOL2 |
O:2/9 |
The solenoid for actuating the cap pusher in the capping station |
Design of the filling system
Remember that we already have the status and all information about the incoming bottles saved in data files from the last two tutorials named bottle project. So you can stop by these previous two tutorials to feed your memory we the information you are going to use here. Now, we need to decide which bit to use to control the filling tube and valves and manage the filling station. Yes, by noticing the filling scenario depicted in figure 3, you can see, everyone, all that we need is the bit at the filling actuators and the bottle size. So let’s clarify by discussing the ladder logic code we wrote for the filling process.
Filling process ladder logic code
Figure 4 shows the few ranges that implement the task of controlling the bottle filling. In the first rung, we added all the conditions at which the main conveyor should stop as a normally closed contact to stop the conveyor from moving while capping, filling, and processing. In the following range, we use the existence bit to ensure there is a bottle to fill and not broken and one-shot instruction to fire the extend the cylinder of the filling actuator. And the following two lines, we activate the large-size bottle valve when the bottle we fill is large or start the one for filling the small-size bottles. And finally, we complete the process by returning the piston of the filling actuator once the bottle, either the small or the large, is filled.
Testing the filling process
As you can see, the filling ladder logic code that we wrote can manage the filling for both bottle sizes, the small with the violet-coloured liquid and the large with the orange-coloured liquid. By identifying the correct position of the bottle at the filling actuator and the right size, the code opens the correct valve to fill with the appropriate liquid for each bottle type. Now, it’s the turn to handle the capping station work. So let’s go doing it; it’s pretty easy!
Capping station design and ladder logic coding
Similarly, we need to identify the correct bit at the capping station and check that it exists, is filled, and is not broken. Thereby we can command the capping actuator to do capping the bottles. Figure 6 shows the simple ladder logic code that handles the capping process. SiIts checked that the bottle was there and not broken. Afterward, it uses one-shot instruction to fire the capper actuator. And the following range unlatches the capper actuators once it has reached its target, thanks to the extended limit switch. Now let’s check the correctness of the code we just wrote.
Figure 7 shows the results of successfully running the whole process filling and capping process. You can see my friends when bottles come to the filling actuator; they are filled with the appropriate liquid based on the bottle size. When they reach the exact position where the capper is mounted, the capper actuator is activated to process the capping successfully.
What’s next???
I’d love to say thank you, my friend, so much for following up with me and my tutorial up to that moment. I hope you have learnt something that increases your knowledge of ladder logic programming and that you have enjoyed practicing one project from the entire industry. We do nothing but bring what we have done in our practical life in industry in the form of tutorials and simulations to take you close to what is going on in the factory every single day for you become familiar with whatever you will see in your future work. For what is incoming? Without question, I will bring a new project from the factory and enjoy learning and practicing together. So stay safe and be ready to meet very soon.