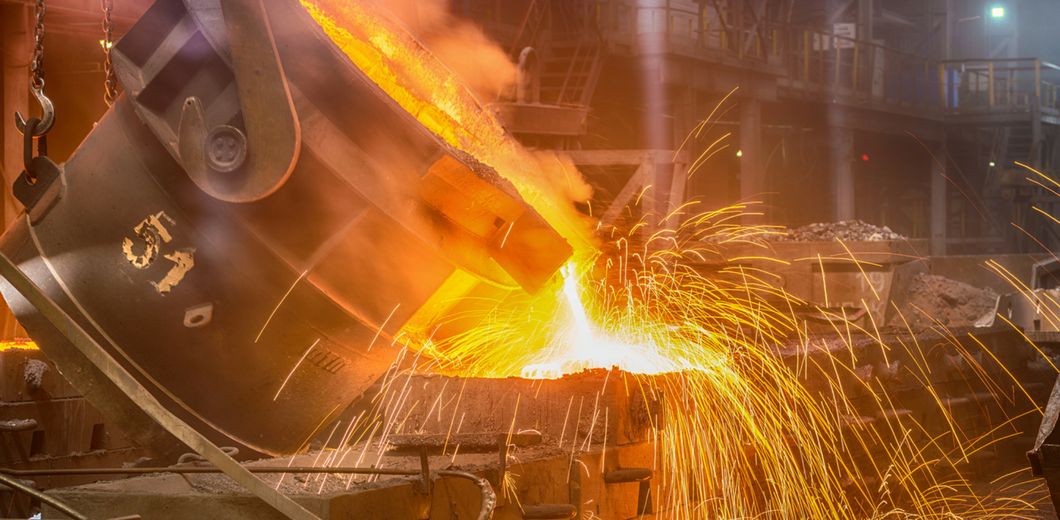
Metal fabrication refers to the manufacturing of sheet metal and other types of metal to fit different shapes.
The metal fabrication industry is vital to a wide range of industries. That’s due to the reliance on metal fabrication for vehicle parts, train tracks, building equipment, electrical devices, etc. A metal fabrication shop has various pieces of equipment needed to design and fabricate a myriad of metals. So, what, then, is custom fabrication?
What is Custom Metal Fabrication?
Custom metal fabrication refers to the production or fabrication of a range of metals to meet unique specifications. Custom metal fabrication projects are carried out for a specific purpose. It involves cutting, bending, rolling, or joining metal to create custom complex shapes based on specific requirements.
Unlike traditional metal fabrication, custom metal fabrication offers more flexibility to meet the product specifications for various industries. It can be used to create tools for construction, mining, aerospace, and energy delivery systems .
3 Benefits of Custom Metal Fabrication
Custom metal fabrication offers certain benefits over stock metal fabrication. It can be used to create precise fabrications for use in rail systems, building equipment, automobiles, and many other purposes.
Here are three major benefits of custom metal fabrication:
Improves Product Quality: You can produce durable metal products through custom fabrication. Metal fabricators consider the best materials that can suit the desired application.
Factors such as external forces, stress, and possible strains are also considered during the production process. For custom metal fabrication, the design is application-centered. The custom metal fabricator uses materials that can ensure increased product quality.
Increases Metal Fabrication Efficiency: Instead of using mass-produced metal works for certain services, custom fabrication drives efficiency by producing specialized designs. It allows for the creation of metal structures using a process that suits the requirements the most.
This helps increase efficiency and reduce the time spent on metal fabrication. Also, custom fabrication allows for optimized product processing and product flow. It makes the best use of metal fabrication materials in the production line.
Offers High Component Compatibility: Another major benefit of custom metal fabrication is the high component compatibility it offers. In custom fabrication, the metal works are designed to meet the required specifications, making them compatible with each other. With custom metal fabrication, you can produce custom shapes that work with the hardware you are using.
Different Types of Metal Fabrication Processes
There are different types of metal fabrication processes. These processes are unique and are utilized based on part geometry, the metal fabrication materials, and the purpose of the product. Below are the common types of metal fabrication processes.
Casting: Casting involves pouring molten metal into a die or mold. The molten metal then cools and hardens into the desired shape. Casting is ideal for the mass production of metal parts with the same shape, for example, in the production of train tracks.
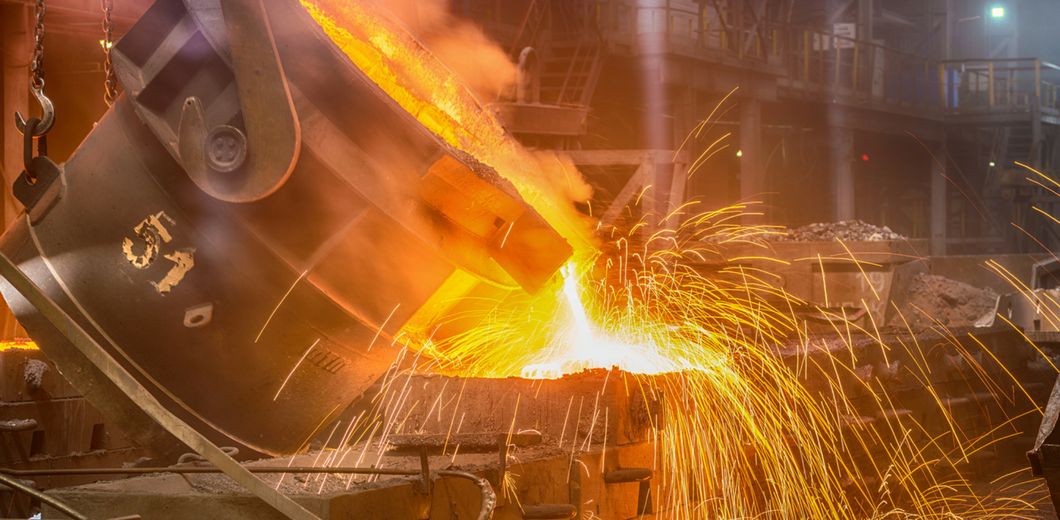
The mold can be reused multiple times to create metal works that are of the same shape. There are different types of casting processes, such as die casting, permanent mold casting, and sand casting.
Cutting: Cutting is one of the most common metal fabrication processes. It involves cutting a large piece into smaller pieces of metal. While sawing remains the traditional and earliest method of cutting, there are other methods, such as laser cutting, waterjet cutting, and plasma arc cutting, among other modern cutting techniques.
Cutting can be done through manual and power tools or through computer-controlled machines. Usually, cutting is the first stage in a metal fabrication process.
Drawing: In drawing, a piece of metal is pulled through tensile force. It is then stretched into a thinner shape. Drawing can be performed at room temperature or at heated temperature. It is known as cold drawing when it is done at room temperature.
However, the metal can be heated to reduce the tensile force needed. Drawing is usually combined with sheet metal fabrication to create box-shaped or cylindrical vessels.
Drilling: In drilling, a rotary cutting tool is used to cut holes in a piece of metal. The drill bit rotates very fast to make a hole in the metal.
Extrusion: In extrusion, the piece of metal is forced between or around a closed or open die. The diameter of the metal will be reduced to the cross-section of the closed or open die if it is forced through.
However, if the metal is forced around a die, it will result in a cavity. The two methods involve a metal slug and a ram to perform the process. Usually, the resulting product is used for piping or wiring. For example, it can be used to create splice kits needed to splice cable.
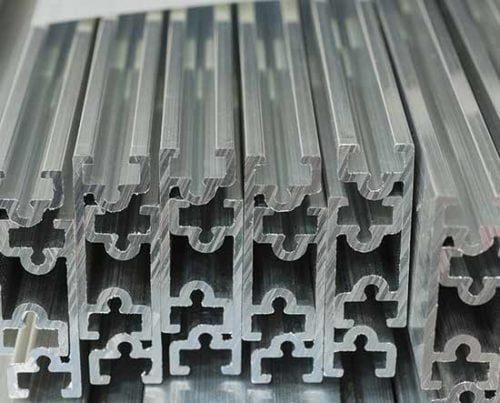
Extrusion can also be used to create short or long metal pieces. Also, it can be performed at room temperature or at increased temperatures. Cold extrusion is typically used for steel metal fabrication, while hot extrusion is commonly used for copper fabrication.
Forging: This involves the use of compressive force to create metal pieces. The metal fabricator uses a hammer or die to hit the workpiece until it forms the desired shape. It can also be done using high-pressure machinery.
Milling: Milling involves using rotating cutting tools to make perforations into the metal until it forms the desired shape. Usually, milling is done as a finishing or secondary process. It can be done through a CNC machine or manually. There are different types of milling, such as climb milling, form milling, angular milling, and face milling.
Punching: Turrets with unique shapes hit the metal to create metal pieces with holes or shaped metal pieces. It can be used to create delicate metal decorations or for other purposes.
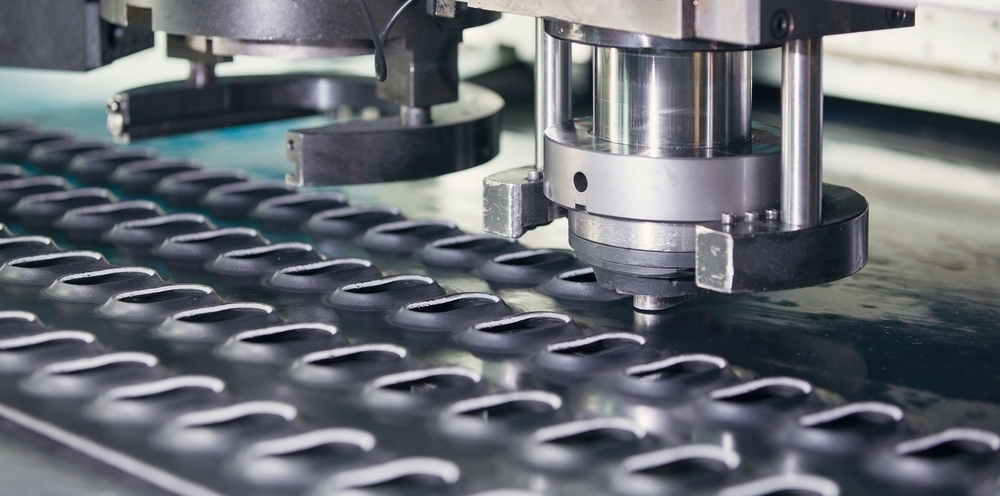
Turning: In turning, a lathe is used to rotate the metal, while a cutting tool is used to shape the metal radially while it spins. The angle of the cutting tool can be adjusted to make different shapes.
In Closing
The metal fabrication industry caters to many other industries. Metal works are used for different applications, such as rail works, buildings, and other projects. Custom metal fabrication involves applying metal fabrication processes to make specific metal works.
The major benefits of custom metal fabrication are improved product quality, increased metal fabrication efficiency, and high component compatibility. The unique metal fabrication processes are used for different purposes to create specific products. It is important to look for experienced companies with specialized equipment when looking for a metal fabrication service.