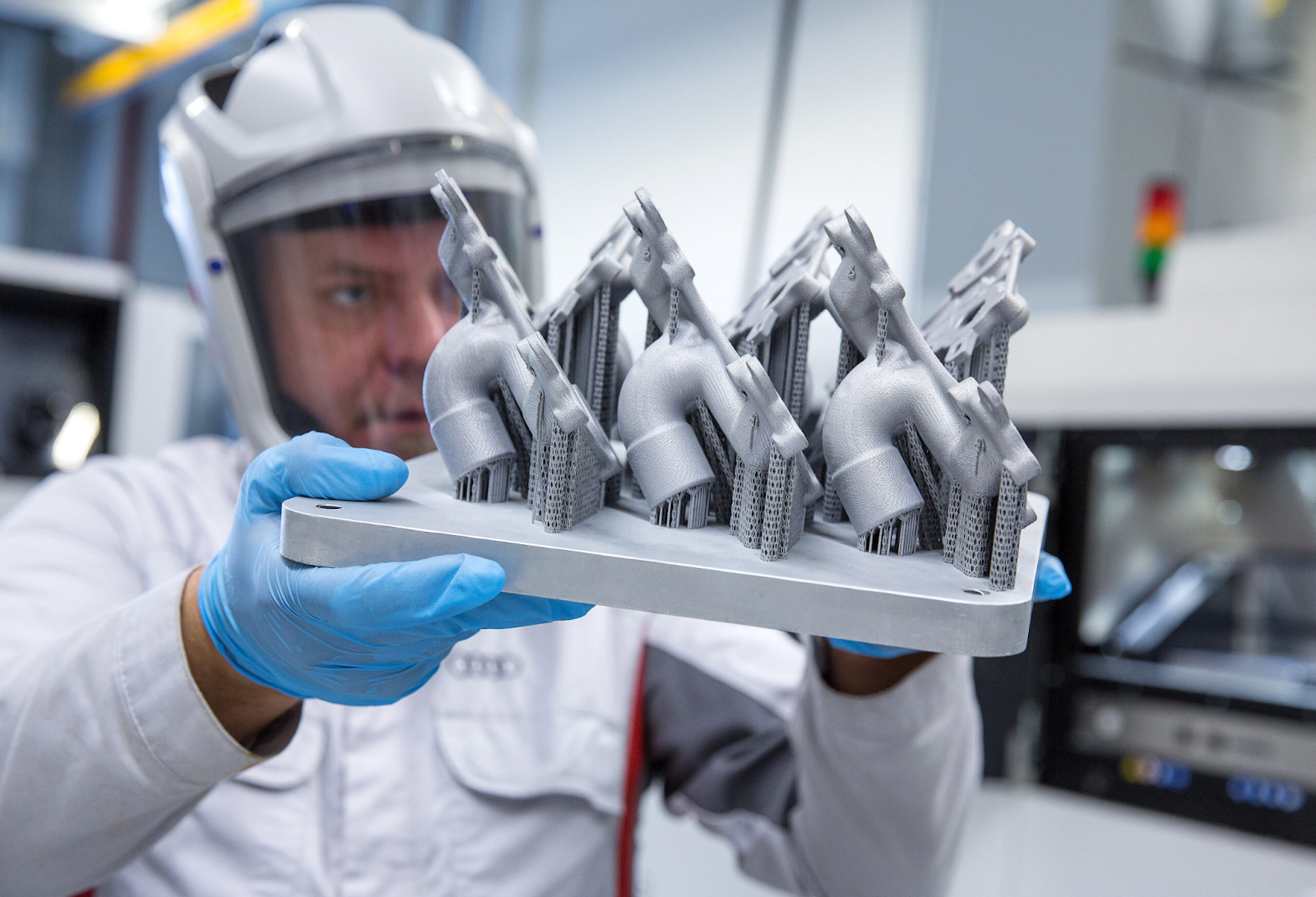
, In recent years, additive manufacturing (AM) has become an increasingly popular topic in the aerospace industry. Additive manufacturing is the process of making three-dimensional objects from a digital file. It is also known as 3D printing.
In general, additive manufacturing builds objects by adding successive layers of material. This is in contrast to traditional manufacturing methods like machining or milling, which involve removing material from a block of metal or other material.
With technology evolving and becoming more widely adopted, additive manufacturing has transformed how aircraft are designed, built, and maintained.
This article will discuss some of the critical benefits of aerospace additive manufacturing.
1. Increases Product Complexity From Fewer Parts
Additive manufacturing provides greater design flexibility than traditional manufacturing methods. This is because AM enables the creation of parts with highly complex shapes and geometric structures that would be impossible to produce using subtractive processes like machining.
And this opens up new possibilities for engineers in aircraft design, leading to more innovative and efficient solutions.
For example, the most common type used in aerospace applications is called selective laser melting (SLM). SLM uses a laser to melt the metal powder into the desired shape. The advantage of SLM is that it can create complex aerospace components and shapes that would be difficult or impossible to create using traditional methods.
Here is an example of a complex design made through SLM.
Previously, products were made by assembling a wide range of individual parts. With additive manufacturing, products can be created using fewer individual parts since the designs are printed using a 3D printer at a time. This allows for more complex designs and saves time you’d otherwise spend in traditional assembling.
2. Reduces Manufacturing Costs
Aerospace manufacturers are always looking for ways to reduce manufacturing costs. One major way to achieve this is by adopting the aerospace additive manufacturing alternative. According to a survey conducted by Appendix, cost-effective manufacturing is among the most important benefits 3D printing offers to aerospace companies.
AM contributes to cost savings by creating complex designs with fewer steps and structural components. Traditional manufacturing methods waste a lot of material because it is impossible to use in the finished product. With 3D printing processes, only the amount of needed material is used, making it more efficient.
Also, additive manufacturing allows for greater customization, leading to reduced costs. For example, if a part needs to be made for a specific application, aerospace additive manufacturing can be used to create a part that is off the shelf. This saves the manufacturer from having to order custom parts from your aerospace suppliers , which can be expensive.
Additive manufacturing is generally much faster and more efficient than traditional manufacturing methods such as milling or casting. Besides the speed, it can produce parts with high accuracy and repeatability. This is because AM eliminates the need for tooling or molds, and parts can be produced layer by layer directly from digital 3D printing models with minimal material waste.
3. Minimizes Storage Requirements
Storage requirements for aerospace equipment differ depending on the application. Some standard storage requirements include:
Temperature control: The equipment must be stored within a specific temperature range to prevent damage or malfunction.
Environmental protection: The equipment must be protected from harmful elements such as dust, moisture, or corrosives.
Storage requirements in the aerospace industry vary depending on the type of aircraft. However, aerospace industries are constantly looking for ways to reduce storage requirements, as storage space is a valuable commodity in this industry.
Additive manufacturing processes help minimize storage requirements by producing parts directly from a 3D printing model.
This reduces the required inventory since parts can be printed on demand instead of on storage carousels, as shown in the image below. Carousels are more common in traditional factories due to subtractive manufacturing methods, such as milling and turning, requiring much material and storage.
With aerospace additive manufacturing, parts are built up one layer at a time, so very little material is wasted. This means less storage is required to store the raw materials freeing up valuable space in factories.
4. Decreases The Weight Of Components
Component weight is a critical factor in the aerospace industry. Every pound of weight eliminated from a single component allows for carrying additional payload or fuel, increasing the aircraft's range or performance.
In recent years, aerospace additive manufacturing has emerged as a promising technology for reducing the weight of aerospace components in the aerospace industry.
Additive manufacturing can create parts that are lighter and stronger than those that can be produced using traditional methods. This is because the additive manufacturing process does not require traditional cutting, drilling, or welding methods. As a result, less material is needed to produce a single component, which reduces its weight.
AM also allows for greater control over the process of manufacturing and chemical microstructures of materials. As a result, components can be designed with specific attributes like improved toughness or fatigue resistance. This reduces weight and decreases fuel consumption and emissions while improving performance and range simultaneously.
Finally, unlike traditional manufacturing, additive manufacturing enables general component design optimization, which helps with weight reduction. The result is lightweight structures. In traditional manufacturing methods, excess material must be added to compensate for errors and inaccuracies in the manufacturing process, resulting in heavier structures.
In Closing
The aerospace industry is a critical part of our economy and our way of life. It produces and operates various aircraft, from commercial airliners to military aircraft. To keep up with the demanding needs of this industry, manufacturers are always looking for ways to improve their mechanical performance. One way that they are doing this is by using additive manufacturing technology.
Additive manufacturing has a transformative effect on the aerospace industry thanks to its many benefits, such as increased product complexity, reduced manufacturing cost, minimized storage requirements, and decreased weight of components.
As 3D printing technologies continue to evolve, more additive manufacturing applications will likely be found in aerospace, leading to an even more significant impact on the industry.
However, 3d printing technology is still relatively new, and there are not many standards in place. In addition, each manufacturer has its additive manufacturing processes and methods for creating parts, making it difficult to know if a part will meet the required specifications.