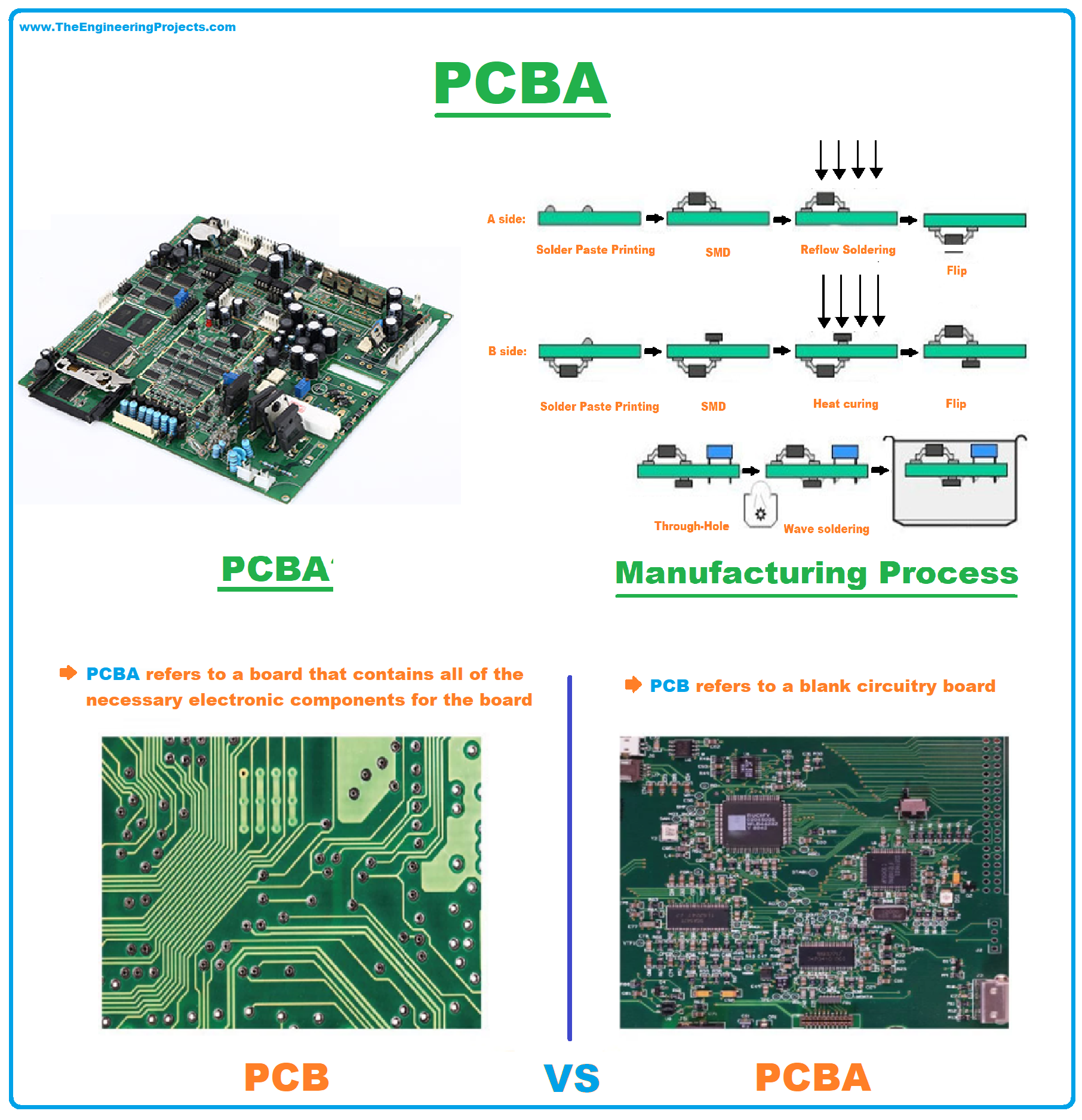
PCBA: Definition, Types, Material, Manufacturing Process, Price & Applications
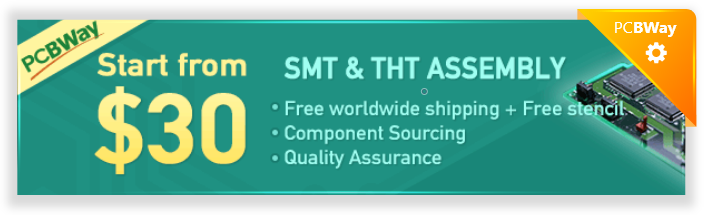
Hey Guys! Hope you’re well. I welcome you on board. In this post today, I’ll walk you through PCBA (Printed Circuit Board Assembly) in detail. It's our 4th tutorial in the PCB learning series.
In the 1st tutorial, we studied printed circuit board(PCB) in detail and learned that PCB provides physical support and electrical connection through conductive copper layers for the electronic components placed on the board. We have seen in our previous tutorials that when we place our PCB order on some PCB fabrication house, they provide us with a PCB board without electronic components. We have to solder the electronic components on the board. But now these PCB companies also offer a service to provide finished PCB boards with electronic components attached. Such a finished PCB board with electronic components is called PCB Assembly(PCBA).
You can place these components by yourself, if you know how to solder them on the board or you can outsource it to the PCB company for the smooth insertion of these components on the boards without compromising the quality of the PCB. Curious to know more about PCBA? Keep reading.
PCBA Definition
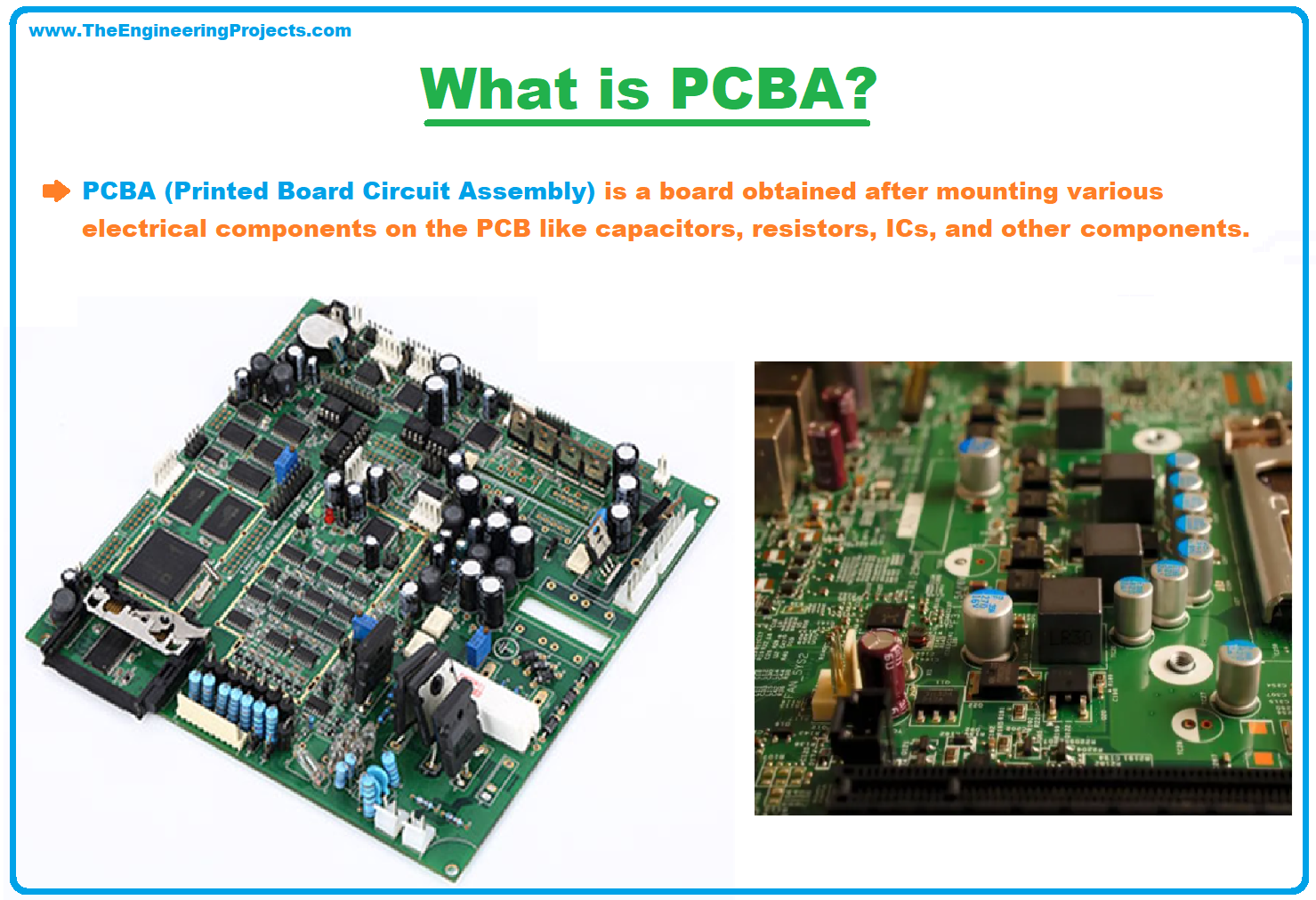
- PCBA(Printed Circuit Board Assembly) is a complete PCB board, where electronic components are mounted by the PCB company.
- Several steps are involved in the Printed Circuit Board Assembly manufacturing process.
- Each step must be in harmony with the next one to ensure a seamless production process for getting a quality final product.
- A PCBA normally passes through a reflow furnace heating to develop a mechanical connection between the components and the PCB.
Let's have a look at the Manufacturing process of PCBA in detail:
PCBA Manufacturing Process
The PCB undergoes DFM(design for manufacturability) check before the actual PCBA process even starts. The DFM check cross-checks the final PCB structure with the initial blueprint of the design. This check identifies any missing links or potentially redundant and problematic features in the final PCB design.
[TEPImg6]
If PCB doesn’t undergo this check, the PCBA process can create trouble in properly mounting the components on the board and maintaining a flawless electrical connection between them. DFM checks not only reduce the cost of the manufacturing process but also ensure the overall functionality of the PCB.
PCBA production process comes with the following steps.
-
Solder Paste
Before adding components on the board, a solder paste is added to the areas, where components rest on the finished PCB. The solder paste comes with greyish tiny balls of metals and is mixed with the flux that turns to a chemical composition and should be added in the right amount & in the right areas of the board.
To add the solder paste, a mechanical fixture is used to hold both the PCB and solder stencil in place. An applicator then takes the solder paste in precise amounts and places it on the desired PCB areas. The machine rolls the solder paste evenly on the intended PCB areas. As the stencil is removed, the solder paste sits on the desired areas.
-
SMT Assembly
After properly adding the solder paste on the board, the board is then passed through the pick and place process, where the robotic machine is used to pick the surface mount components from the reels and place them on the intended areas of the board.
The components added remain in the desired areas due to the sticky feature of the solder paste. The solder paste comes with enough bond strength that keeps the components in place.
Earlier this procedure was practiced manually by humans. However, the inception of advanced technology removed the need for this erratic manual process, since the automated process by machines is more accurate and efficient than the traditional manual process.
-
Reflow Soldering
Once the electronic components have been placed in the desired locations, they remain there due to the presence of solder paste. The board then undergoes a Reflow Soldering process that solidifies the solder paste to keep the components at the required positions.
In this process, the finished board is transferred to a conveyor belt that passes through a big reflow oven having a series of heaters; the temperature of these heaters stays around 250oC which generates gradual heat to bake the board. At this stage, the temperature is high enough to make the solder melt, keeping the components tightly in place.
Once the solder has been melted down, the finished product is then passed through a series of cooler heaters that cools down the melted solder paste, giving it strength and creating a permanent solder joint to firmly connect the surface mount components with the board.
This is the reflow soldering for the one-sided PCB. Know that for two-sided PCB the stenciling and reflowing will be done separately for each side.
-
Inspection
Once the reflow soldering has been done, the assembled board undergoes a proper inspection where the functionality of the board is tested. As the PCB passes through a reflow soldering process, it may result in poor connection quality or in worst cases, the elimination of the entire connection. To check these problematic features and common errors, the assembled board undergoes a careful inspection.
- Optical Inspection: Recognize that, manual inspection is not an option for inspecting hundreds of surface mount components on the boards, instead, automatic optical inspection is exercised to look for the defects and errors in the board. In optical inspection, an automatic optical machine is used that comes with high-powered cameras that are located at different angles to monitor the connections. The solder connections reflect light at high speed with different intensities, allowing the machine to analyze the connections of lower quality.
- X-Ray Inspection: For complex and layered circuit boards, the X-ray inspection method comes into play, where X-rays are used for the inspection. With X-rays, layers become transparent, helping you see through the layers and identify the common problems on the board. These inspections are carried out before the final functional test inspection which involves the steps to make sure the board is fully functional and does the job perfectly.
-
Plated Through Hole Components
Based on the type of PCB board and the components used, the PCB assembly may go beyond the scope of SMT components insertion. In that case, Plated Through Hole(PTH) components insertion is used, where holes are drilled on the board and go completely through the board establishing a conductive path from one side of the board to another. Solder paste is not used in this case because it won’t stick and creeps into the drilled holes. In this PTH process, two types of soldering processes may be used:
- Manual Soldering: This soldering is manually done by humans. In this process, one person at the station is given the task to insert components in the desired PTH area. Once finished, the board is transferred through a conveyer belt to another station where another person is destined to insert another component. The cycle continues until each hole is filled with the desired component.
- Wave Soldering: Wave soldering is an automatic process. Once the PTH components are placed on the desired hole areas, the board is transferred through a conveyer belt that passes through a special oven that smears the layer of melted solder on the bottom of the board, soldering all pins at once.
-
Functional Test
In this process, the finished product undergoes the final inspection called the ‘functional test’ where simulated power signals run through the PCB to analyze the electrical characteristics of the board. If voltage, current or signal output in these characteristics show sudden fluctuation beyond the permitted range, it means the board has failed the test.
-
Feedback
It is important to investigate any failures to guarantee the functionality of the manufacturing process. The recommended place to monitor the output and the potential errors is the optical inspection stage because errors are detected and rectified at this stage. This saves time ^ & money and avoids PCB production with similar defects.
Where to place PCB Assembly order?
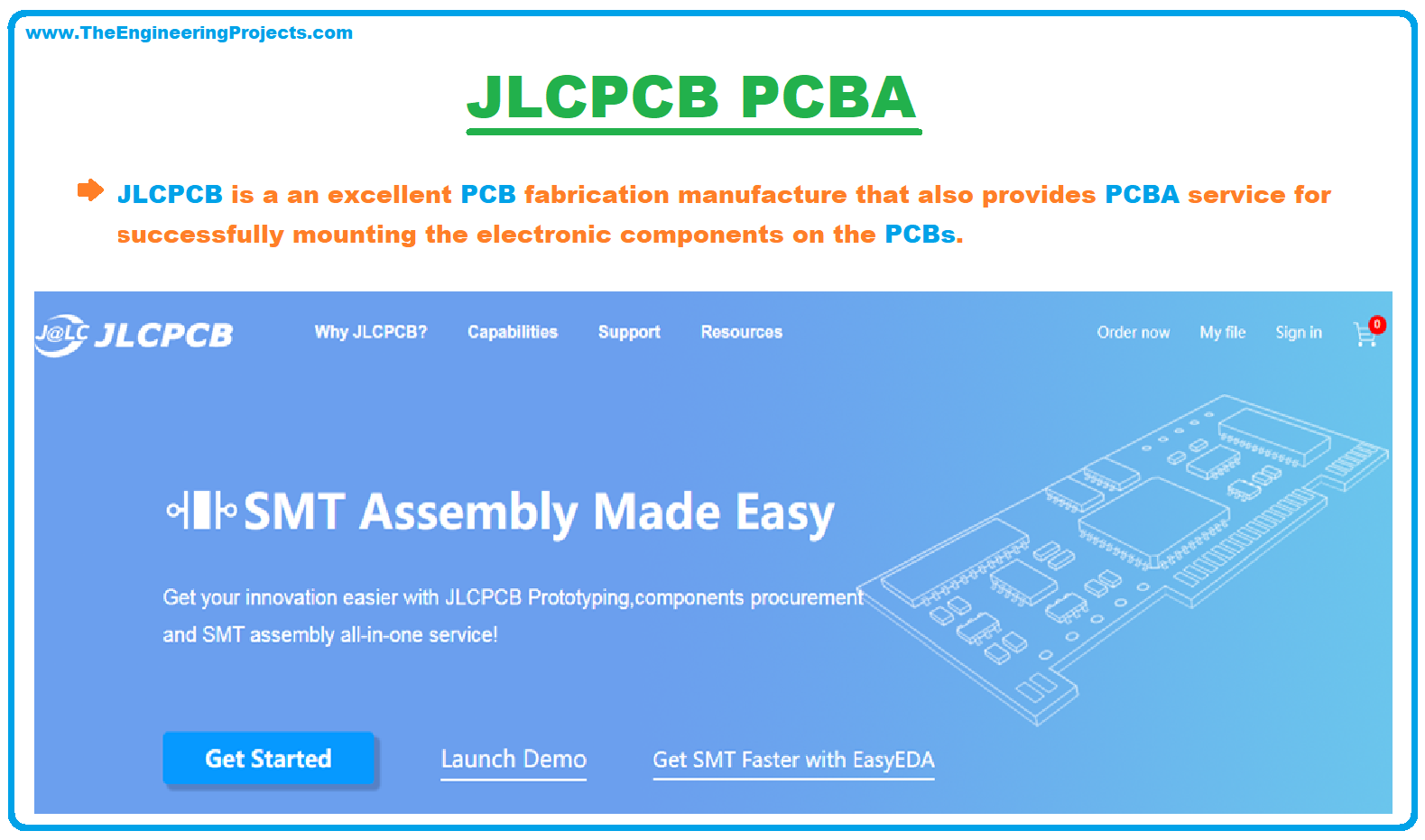
- JLCPCB is an excellent PCB fabrication house that also provides PCBA services.
- From solder paste printing and SMT to reflow soldering and optical inspection, the board goes through every step with careful scrutiny, ensuring top-quality finished PCB assembly with electronic components.
- If you’re looking for reliable and economical PCBA service, you should give JLCPCB Fabrication House a try, you won't regret it.
PCBA Pricing Factors
- The price of PCBA is obviously more than the manufacturing of a simple PCB board. In PCBA, electronic components are mounted on the PCB using SMT technology.
- The size of the circuit board and the number of components that need to be mounted on the board plays a key role in defining the overall cost of the assembled circuit boards.
- Moreover, the total number of holes and their sizes are also important factors while defining the price of the board.
- Similarly adding more layers to the board and the type of material used will influence the cost.
- The customization in the manufacturing process will affect the cost; the more custom features you would like to add to the board, the more the cost.
PCBA Applications
PCBs are the backbone of electronic devices used for commercial and domestic purposes. More often big electronic companies don’t spend time in designing the PCB and then separately mounting the electrical components on the circuit boards. They purchase PCBA services, where circuit boards come ready-made installed with the components.
The common PCBA applications include:
- Companies prefer PCBA services for making consumer electronics, calculators, and smart toys.
- PCBA services come in handy in the manufacturing of auto parts.
- Automotive companies buy PCBA services to install circuit board assemblies in the antilock brake system, airbag control, audio-video system, engine timing system, ignition system, and more.
- The circuit board assemblies are used in heart-related applications live developing the pacemakers and heart monitoring devices.
- Military and defense systems prefer PCBA services for making the defense system, aerospace, naval, and aviation applications.
That’s all for today. So far, we have discussed the basics of both PCB and PCBA, now we will have a look at the Top PCB Manufacturers to place your order. Hope you’ve enjoyed reading this article. If you have any questions, you can pop your comments in the section below. I’d love to help you the best way I can. Thank you for reading the article.