In the past, the US Occupational Safety and Health Administration or OSHA came into effect with the sole aim to protect workers in the States. Large corporations and conservative politicians shun the act because they find it interfering and hindering the production of valuable goods and services.
During the Trump presidency, the president nominated a director for the regulatory body, but the Senate never confirmed the position, and the slot remained vacant. While the OSHA situation remains uncertain, companies and employers can ensure worker safety by introducing an effective safety program.
What Is a Safety Program and How To Get Started?
The first step towards construction safety is to refer to the applicable OSHA and state-issued standards for your industry. Thirty-four states have regulations in place for injury/illness prevention programs in the US, including 15 states with compulsory rules for employers.
The next step is to devise a safety program best suited to your workplace and in line with an injury or illness prevention program. An effective safety program would include workplace safety audits, training for health/safety, safety management reporting, claims management, and a lot more.
Once the safety program is drafted with all aspects of the program, The top management should then share the same with all employees (new and old), insurance carriers, and the regulatory agency in your state.
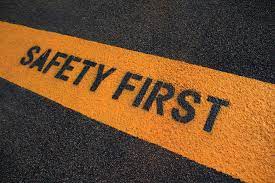
Top Management Should Take the Initiative and Commit
Since a good safety program requires a workspace audit for safety hazards, the top management should be involved and committed to the cause. The commitment of top leadership towards safety and risk management acts as the backbone of any safety program.
The top honchos of the organization should take the initiative and establish safety goals for the company. Once the goals have been established, the management should then delegate the implementation and maintenance of the program to capable individuals.
The top management is also expected to ensure the safety program's success by making necessary resources and professional support available.
Identify and Prevent the Hazards at the Workplace
Once the safety goals for the workplace have been established, the individuals trusted with the execution of the safety program must identify and assess the possible hazards at the premises. In this step, worker participation is of the utmost importance. It'll require honest feedback from the workers to get valuable insights.
Employers should perform a complete workplace inspection to pinpoint any hazard that can be critical. After spotting all risks, the next step is to review the available information on these hazards, including preventive measures, ensuring safety, and emergency course of action.
The employer should also consider any injuries or illnesses that have been reported frequently in the past. This is the best source to single out any workplace hazard and take corrective measures against the same.
After identifying hazards, the employer should elaborate plans to control the existing risks on priority. There should be an interim control to prevent workers from risks that can't be rectified immediately. Only after all safety measures have been implemented and inspected should the work resume.
Conduct Regular Training Programs for the Employees
Training is a crucial part of risk management at work. Training and education workers about potential hazards and their preventive measures should be done regularly. OSHA has a dedicated section on its website for safety and health topics and hazard alerts, which are very useful to arm workers against all sorts of emergencies.
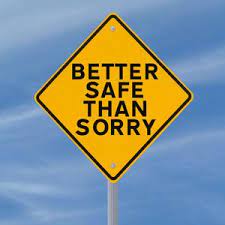
Employers should also conduct regular training programs covering topics like reporting injuries and illness, ways to recognize a hazard, tips to control any danger, and other such crucial information. Continuous training and education will keep your workers safe and prevent any accidents at your workplace.
Evaluate the Program and Its Success To Ensure Continuous Improvement
The top management should continuously review the safety program in place to determine if they are still effective. In case of any loopholes or inefficacy, the employer should make corrections immediately. Also, keep a check on new regulations and new hazards, should they come up.
The best way to streamline a safety program is to bring onboard risk management advisors who know their way around OSHA, state, and local regulations. Select an advisor who knows and understands your business, as it'll help them with a safety program best suited for your workplace.