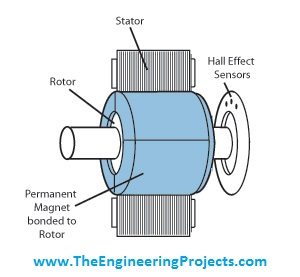
Brushless DC Motor
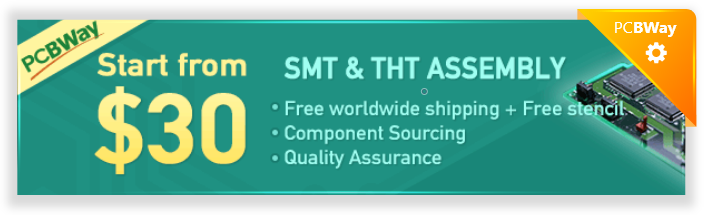
Now in today's tutorial i am going to share a tutorial on one of the type of DC motor which is Brush-less DC motor. Brush-less DC motor is commonly known as Electronic Commutated motor. It is in fact a synchronous motor. From the word DC, one thing becomes clear that the supply voltage will be DC but as i mentioned in the previous line that it is a synchronous motor then, it will need AC supply to run. So what actually happens is that from source DC voltages appears and after the inverter circuit, we get AC voltages and these AC voltages are actually given to the motor to operate. The rotor of a Brush-less DC motor is actually a permanent magnet rotor. While some winding is done on stator. Brush-less DC motors are also commonly known as stepper motor but there is a very little difference in between both these motors and their operation. Like stepper motor are generally used at that placed where they have to stop again and again and the continuous operation of the motor is not required. There is also another big difference between Brush-less DC motor and stepper motor that the rotor of stepper is placed to work in proper angular direction. Now lets get started with the working and applications of Brush-less DC motor
Brush-less DC motor
Brush-less DC has 2 parts. One is called rotor and the other is called Stator. Here the rotor is a permanent magnet and it rotates inside the fixed armature. This assembly gives us a very big advantage which is, that it reduces the heating losses. Rotor is placed inside the stator and this allows the motor to produce more torque. It is our choice to make a brushless DC motor of different poles. For example we can made a motor having 2,3 or poles and all are DC brushless motors. Brush-less DC motor can be made in 2 different design. In first design, the rotor is placed inside the fixed stator. This configuration is also known as 'inrunner' because the rotor is running inside the stator.
While in the second configuration, we have a fixed stator inside and the permanent magnet rotor rotates around it. This type of configuration is called 'outrunner'. We can also place the stator windings in 2 different configurations. If we place the stator winding in delta configuration and we are dealing with a 3 pole motor then, all the windings will be connected in series and the power supply from the source is applied to all the windings. The resulting configuration looks like a triangle shape. While on the other hand if we wish to place the stator winding in Wye (Y) then we will common the one terminal of each winding. And to the remaining 3 terminals, we will connect the power supply to all those three points.(Since we are working with 3 phase motor and we will have three wires and all of them will be phase wires).
Both these winding configurations have their own advantages and they are listed below as:
- If you have made the stator winding configuration in Delta, then this motor will have a low starting torque. Which means at slow speeds it will generate a very low torque and at higher speeds its torque will also increase with speed.
- The Star type stator motor possess high starting torque. At starting or at very low speed it generates much high torque but as the motor picks up speed, it torque doesn't builts up as compared to Delta type motor.
- Efficiency also have a greater impact on the operation and reliability of motor operation. If we compare the efficiecies of both these motors then, we will see that motor having Star shaped winding is more efficient as compared to delta shape winding.
- Reason is that the star shape winding motor have high starting torque and it is able to drag heavy loads even at low speeds.
Control circuit of Brush-less DC motor
As i explained earlier that the supply voltages may be DC but this motor requires AC voltages to operate actually. So, we have a control circuit which allows the motor this kind of operation of the motor on such voltages. Since the control circuit has to rotate the rotor so the control circuit needs to know the position of the rotor in rest position. To cope with this thing, we implement HALL EFFECT Sensor in control circuit. If you are using a 4 pole motor then the controller will energize the 2 coils with NORTH polarity and the other 2 coils with South polarity. When the stator coils will be energized then one set of coils will tends to push the rotor away from it and the other set of coils will tend to attract the rotor to itself, in this way the rotor will start to rotate and a torque will be established in it and afterwards it would be able to pick load.
Practical Applications
Brush-less DC motor possess a large no of industrial applications. Although, these types of motors are little costly and also complex to operate because of the control circuit but still we can't ignore the importance of this type of motor. Some of its industrial based applications are listed below as:- Biggest and most common use is that these motors are used in laptops and computers for cooling purpose.
- An old use of low power and very low speed DC brushless motor was that they were used in gramophones records.
- High rating and bigger size DC brushless motors are used in transport vehicles and also in Hybrid cars.
- These motors may be of small size but have permanent magnet rotor and are able to develop high starting torque.
- In refrigeration and cooling systems, Brushless DC motor is used in all appliances for the condenser cooling purposes. Both large and small air-conditioning systems uses Brushless DC motor.
- When high voltages AC is generated and transmitted, so need a control mechanism for its safe operation and control. Brushless DC motors are also used at those places for proper cooling of micro processors.
- Brushless DC are able to develop high starting torque and gives good speed response. That's why they are widely used in water pumps, fans and variable speed industrial applications.
- These motors are preferred to work in industries because they possess high power density, can give good speed and torque characteristics and also high efficiency.
- Brushless DC motors have good thermal conditions so they are able to operate at variable speed without excessive heating.
- Brushless DC motor have the biggest demand in defense applications. Now a days they are commonly used in helicopter's rotors, because of their favorable power to wight ratio.