I'll try to explain everything related to flexible PCB so that you could get a clear idea of what is this about and what makes it stand out from other PCB boards? Let's dive in and explore the properties of flexible PCB one by one:
What is Flexible PCB?
- For products to place on irregular surfaces i.e. Keypad.
- To utilize the flexible areas of the product i.e. smart wrist-watch.
The most common example of a Flexible PCB is the ATM Keypad. These ATM Keypads are designed using flexible PCB so that they could be easily placed on any irregular surface i.e. circular. Moreover, smartwatches also use flexible PCBs, where PCBs are incorporated in the watch bands and because of this added space, more embedded functions can be installed in the watches. Now let's have a look at a proper Flexible PCB Definition:
Flexible PCB Definition
- Flexible PCB(also called Flex PCB/Flexible Printed Circuits(FPC)) is an advanced type of PCB and has the ability to bend, twist or fold into any shape.
- It's an incredible addition to the electronics industry as it occupies less space and is very lightweight.
- A rigid PCB is relatively easy to handle while processing a flexible PCB requires extra protocols(special clamping, material handling etc.), that's why Flexible PCB is normally costly as compared to other types of PCBs.
- In some electronic projects, both flexible and rigid PCBs are incorporated together to produce a unified product, such PCBs are termed as Rigid-Flex PCB.
- Flexible PCBs are normally used in wearable electronic products as they can easily stick with the body.
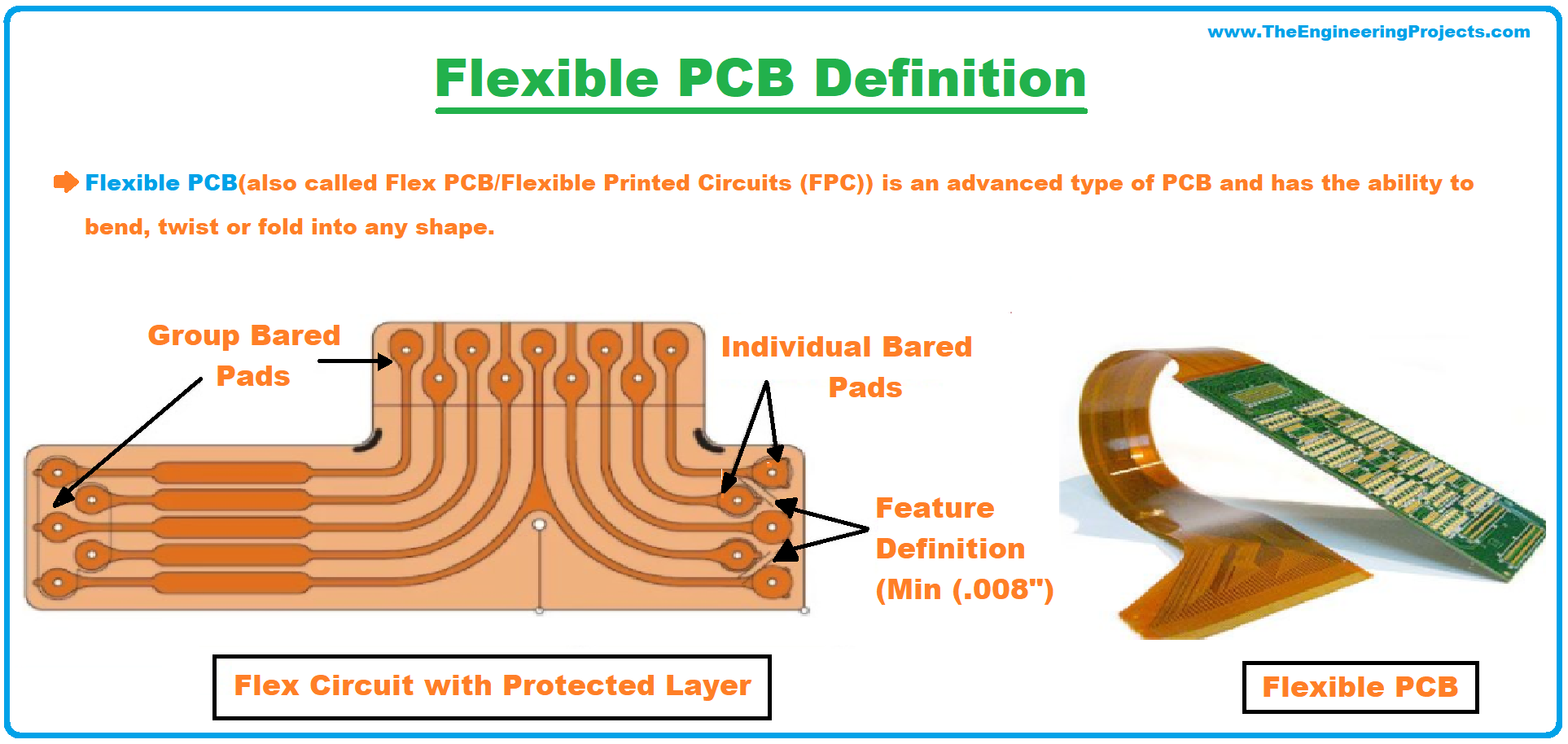
Flexible PCB Key Points
- Flexible PCBs are not that simple/cheap, thus not used by hobbyists or students and are normally designed by companies for their electronic products.
- Flex material must be not too flex or too rigid that it breaks the PCB when it is folded or twisted around the corners.
- Complex flexible products make use of reel-to-reel technology which involves advanced material handling techniques.
Why we need Flexible PCB?
Before Flexible PCB, electronic products were designed using Rigid PCB and in few products(i.e. wrist-watch), space for rigid PCB was almost negligible as compared to its complete size(including bands). To utilize such parts of electronic products(for adding extra technology/circuits), there was a need to bring flexibility in electronic PCB to fit in any shape or place and thus Flexible PCB came into existence.
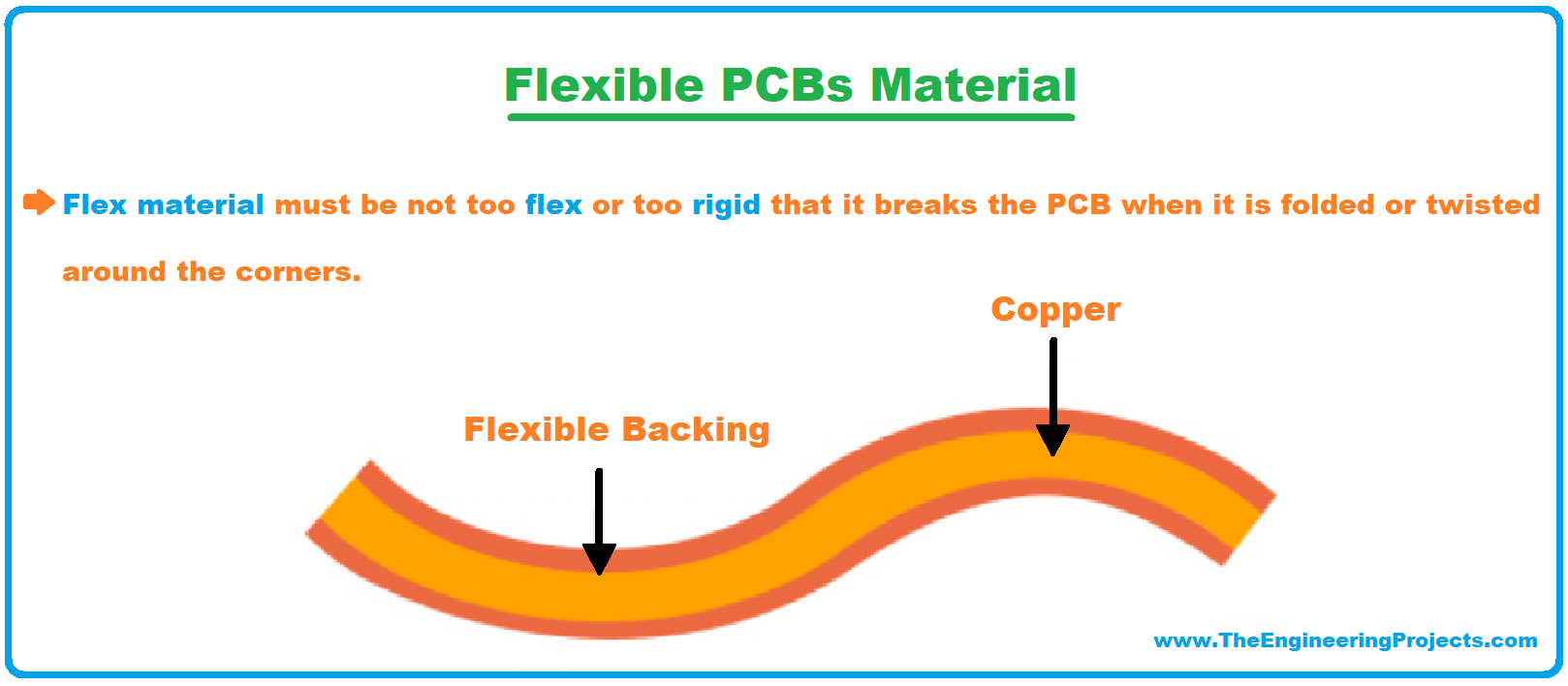
Flexible PCBs have also made electronic products hand-carry i.e. Flexible Computer Keyboard. Simply roll and place it in your laptop bag. Flexible PCBs are also used in Oil & gas sector as they have the capability to sustain high temperatures.
So, now let's have a look at the Manufacturing Process of Flexible PCB:
Flexible PCB Manufacturing Process
The flexible PCB Manufacturing Process involves almost the same steps as that of MultiLayer PCB, although it involves more professionalism & expertise. Let's have a look at the steps of the Flexible PCB Manufacturing Process:
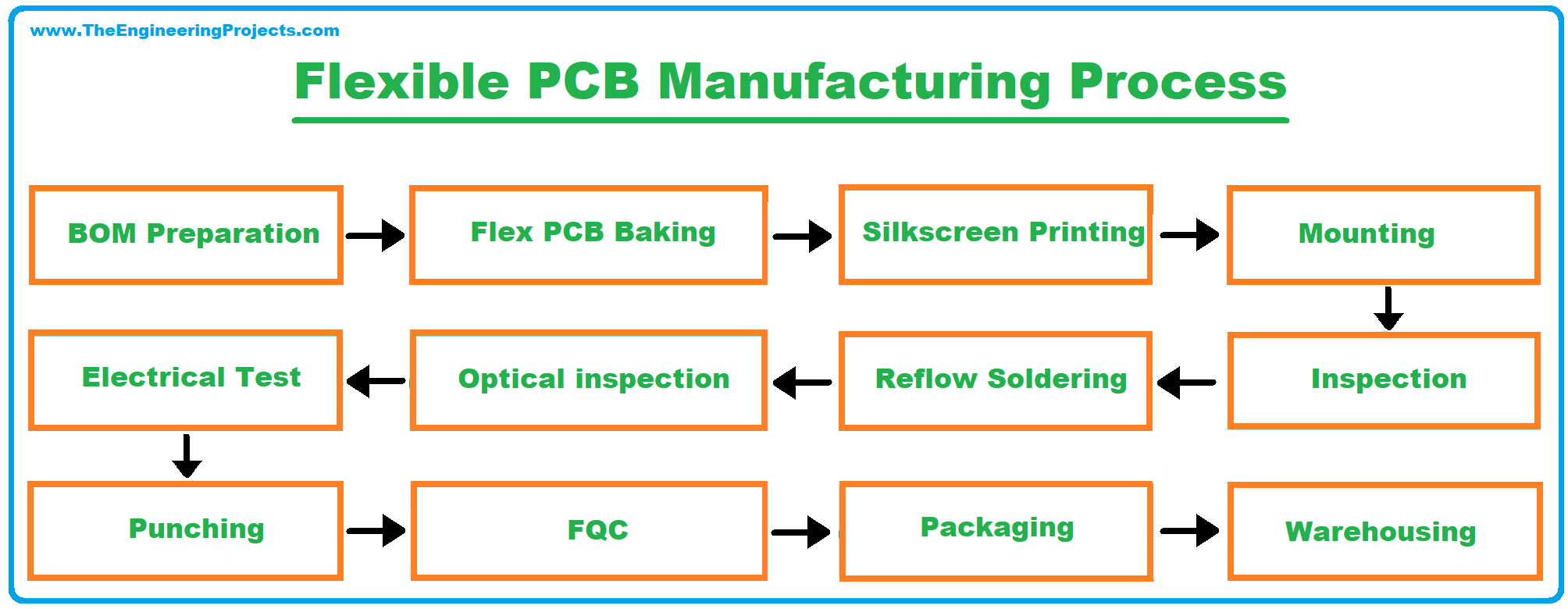
Step 1: Design CAD Model of Flex PCB
- Computer-Aided Design(CAD) models of Flexible PCBs are designed by professional designers.
- Circuit designing of flexible PCB involves multiple teams as there's a lot of factors to decide.
- Apart from designing the electronic circuitry, designers have to take care of mechanical structure & chemical materials as well because stretching or extra bending may harm the fle PCB.
Step 2: Finding Flex PCB Manufacturer
- It's the most important step of all, as we can't design flex PCB on our own, we have to take help from PCB manufacturing companies.
- So, the designers should take extra care in the selection of PCB manufacturers.
- Chinese PCB companies i.e. JLCPCB, PCBWay, WellPCB etc. offer cheap flexible PCB rates.
Step 3: How to manufacture Flex PCB?
Flexible PCBs are manufactured by a PCB company, which takes order from the user(normally designer) and delivers it according to the specified instructions. Here are the steps involved in the Flexible PCB manufacturing process:
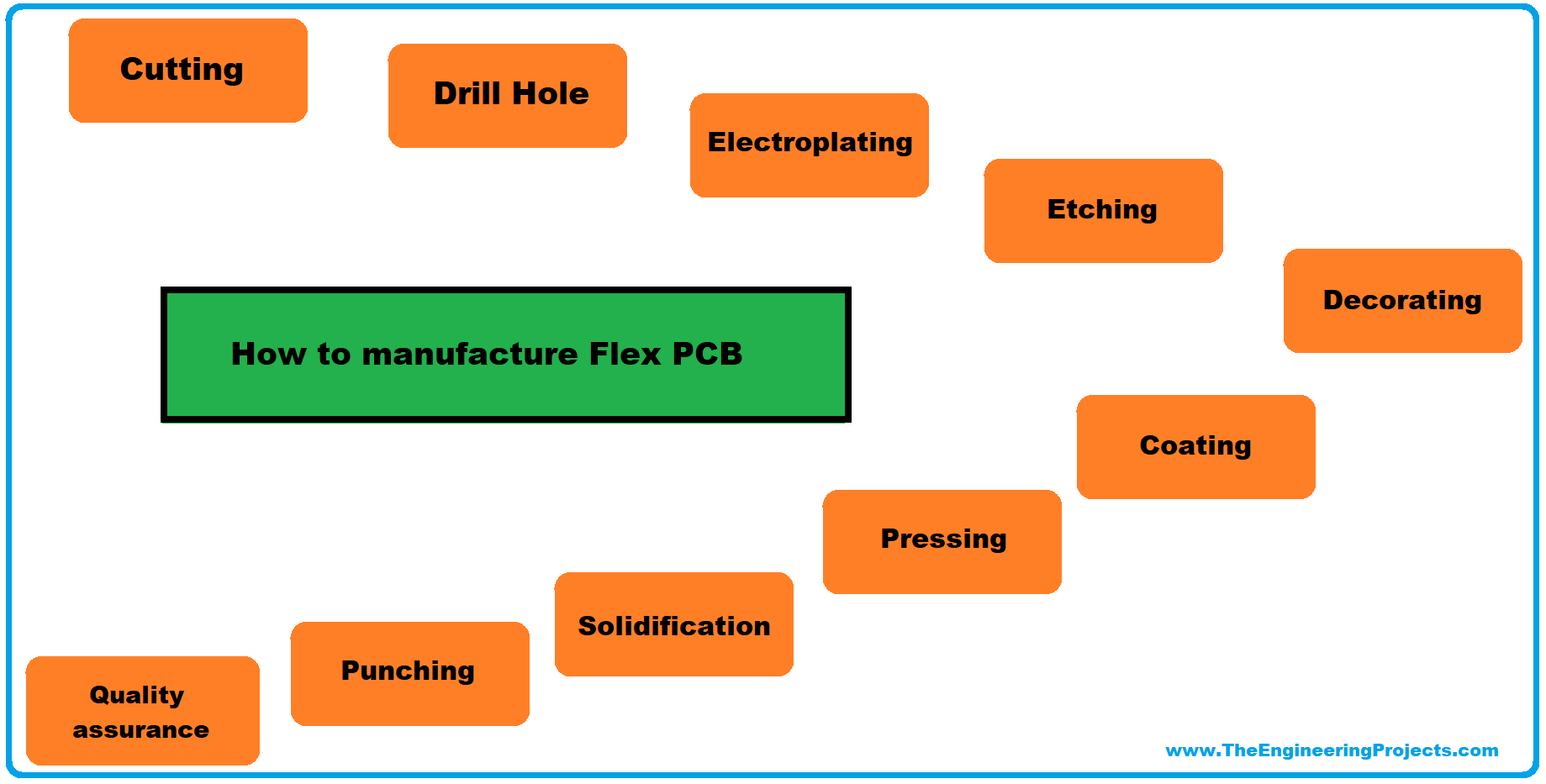
- Cutting: According to specified dimensions in flex design.
- Drill Hole: Drilling of holes and vias(in case of multilayer).
- Electroplating: It involves the placing of coppers tracks or paths.
- Etching: Chemical treatment of Flex PCB.
- Decorating: Involves few touch-ups of flex PCB i.e. bordering.
- Coating: Lamination of Flex PCB.
- Pressing
- Solidification
- Punching
- Quality assurance
- Flex Circuit Overlay is a lamination process that is widely used to protect and encapsulate the external circuitry of the flexible printed circuit.
- Protective film thickness ranges from .0005" to .005", however, .001" and .002" are the most common thicknesses used.
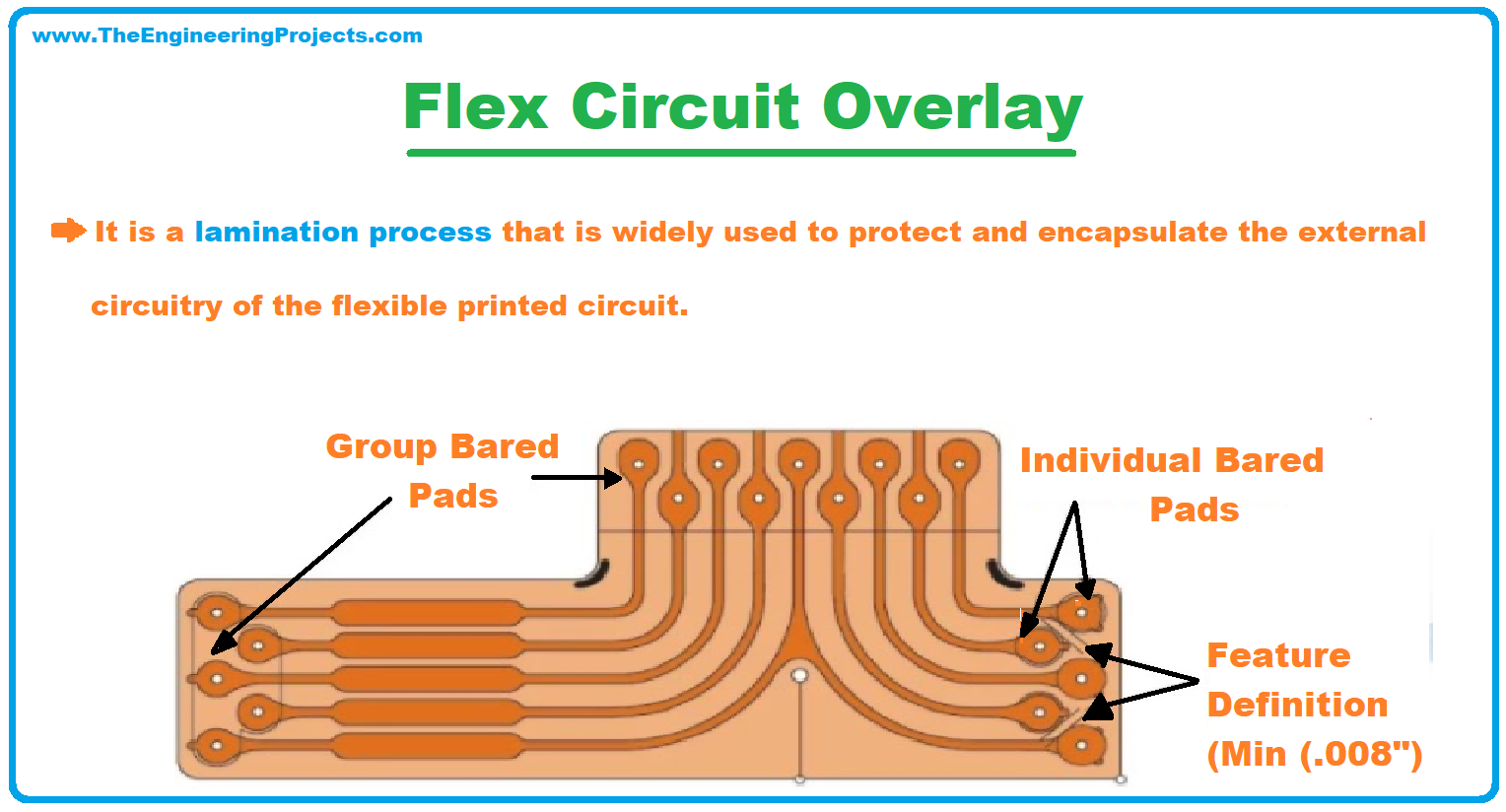
Step 4: Flexible PCB Testing
- Flexible PCB Testing is performed after receiving the order from the PCB company.
- It's normally tested in the prototype project.
Advantages of Flexible PCB
Now let's have a look at the advantages of Flexible PCB:
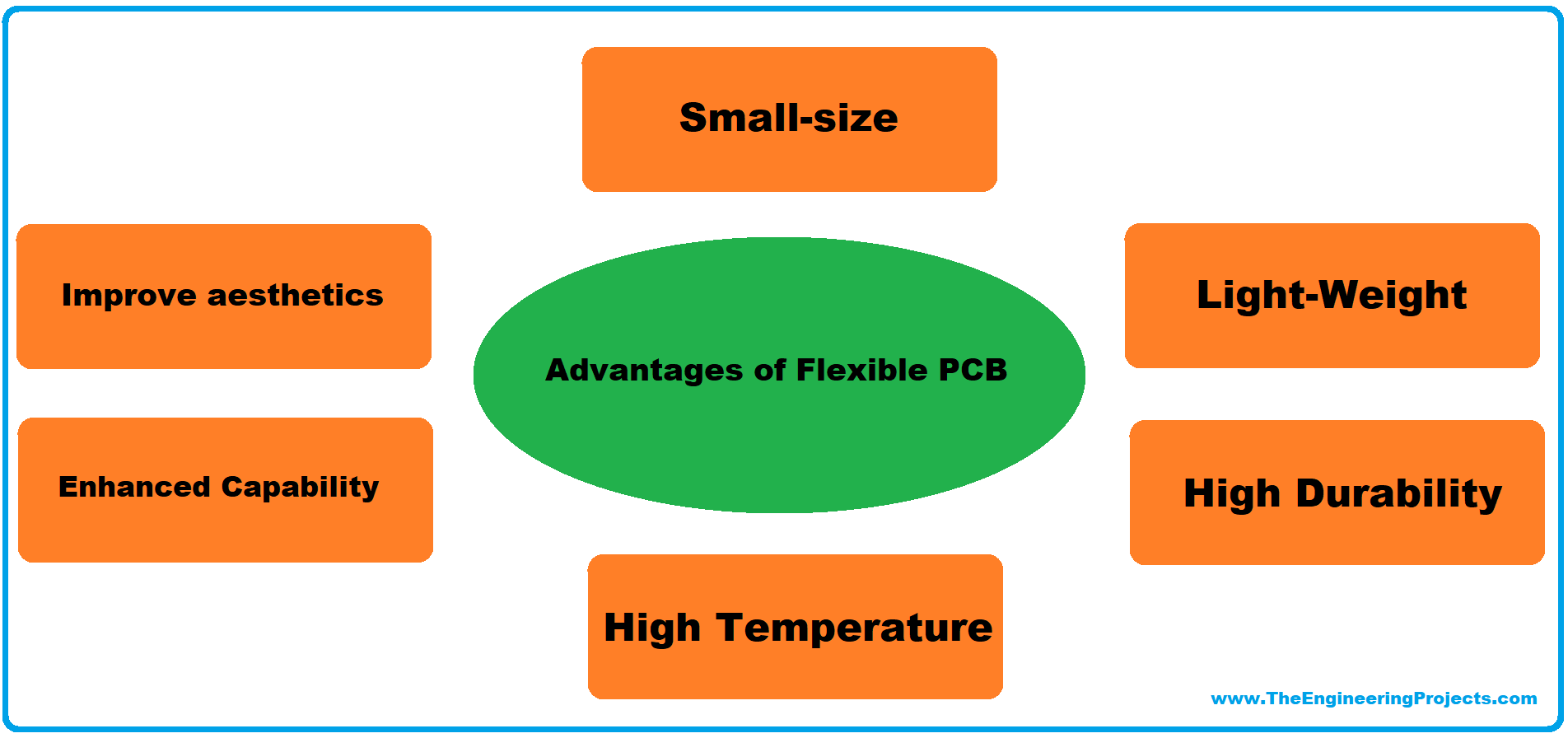
1. Small-size
- Small-size is the main advantage of Flexible PCB and even in some cases, flexible PCBs are simply rolled and adjusted in small spaces.
- They have negligible width as a simple paper.
2. Light-Weight
- Flex PCBs are very light in weight as there's no cardboard(substrate core) present in them.
- Normally its weight is because of SMD components present in it.
3. High Durability
- If treated nicely, Flex PCBs normally have long lives as they are manufactured under precise conditions and in the presence of experts.
- It's also coated with formulated materials which increase its durability.
4. High Temperature
- It can withstand high temperatures and thus used in the oil & gas sector where rigid PCBs may melt out.
- Temperature withstand ability depends on the material used to design it.
5. Enhanced Capability
- Flexible Printed Circuits help in improving the overall performance of electronic products by increasing component density.
- Using Flexible components, we can add more circuitry to our autonomous products, thus enhancing their capabilities.
Now let's have a look at the disadvantages of Flexible PCB:
Disadvantages of Flex PCB
Although Flexible PCBs have a lot of advantages over Rigid PCB but their advantages are specific to certain sectors and thus we can't use them in normal projects. Here are few disadvantages of Flex PCB:
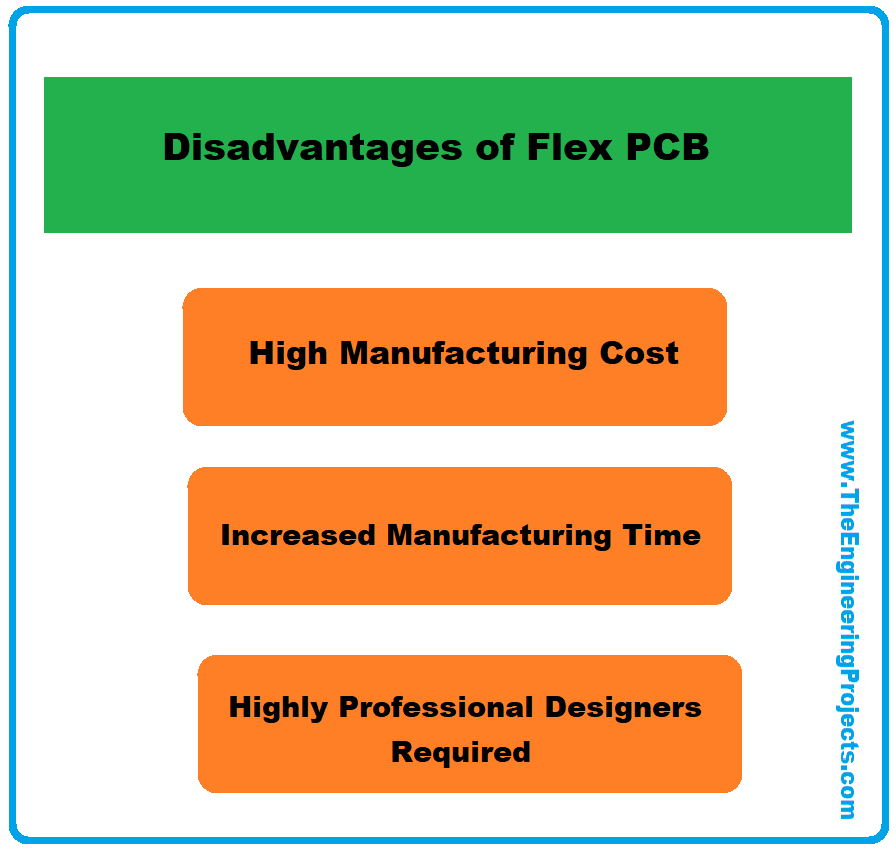
1. High Manufacturing Cost
- Flex PCB has high manufacturing costs, which makes it out of reach for hobbyists & engineering students.
- The Flexible PCB Manufacturing process is not that way and involves chemical materials for coating etc. thus it's a bit expensive.
- Online PCB companies from China i.e. JLCPCB, PCBWay etc. provide competitive rates.
2. Increased Manufacturing Time
- As compared to Rigid PCB, flex PCB requires more manufacturing time as it involves a lengthy process i.e. lamination, coating etc.
- It depends on the complexity & quantity of your products but normally takes a week for a simple order.
3. Highly Professional Designers Required
- Designing a Flexible PCB involves extra care, as if there's any designing error, you have to redo the manufacturing process.
- So, Flexible Printed Circuits are designed by a team of highly professional designers.
- Depending on the complexity of electronic design, it may involve multiple teams.
Applications of Flexible PCB
Although Flexible PCBs are not that common, thus used in specific applications only. A few Flex PCB applications are as follows:
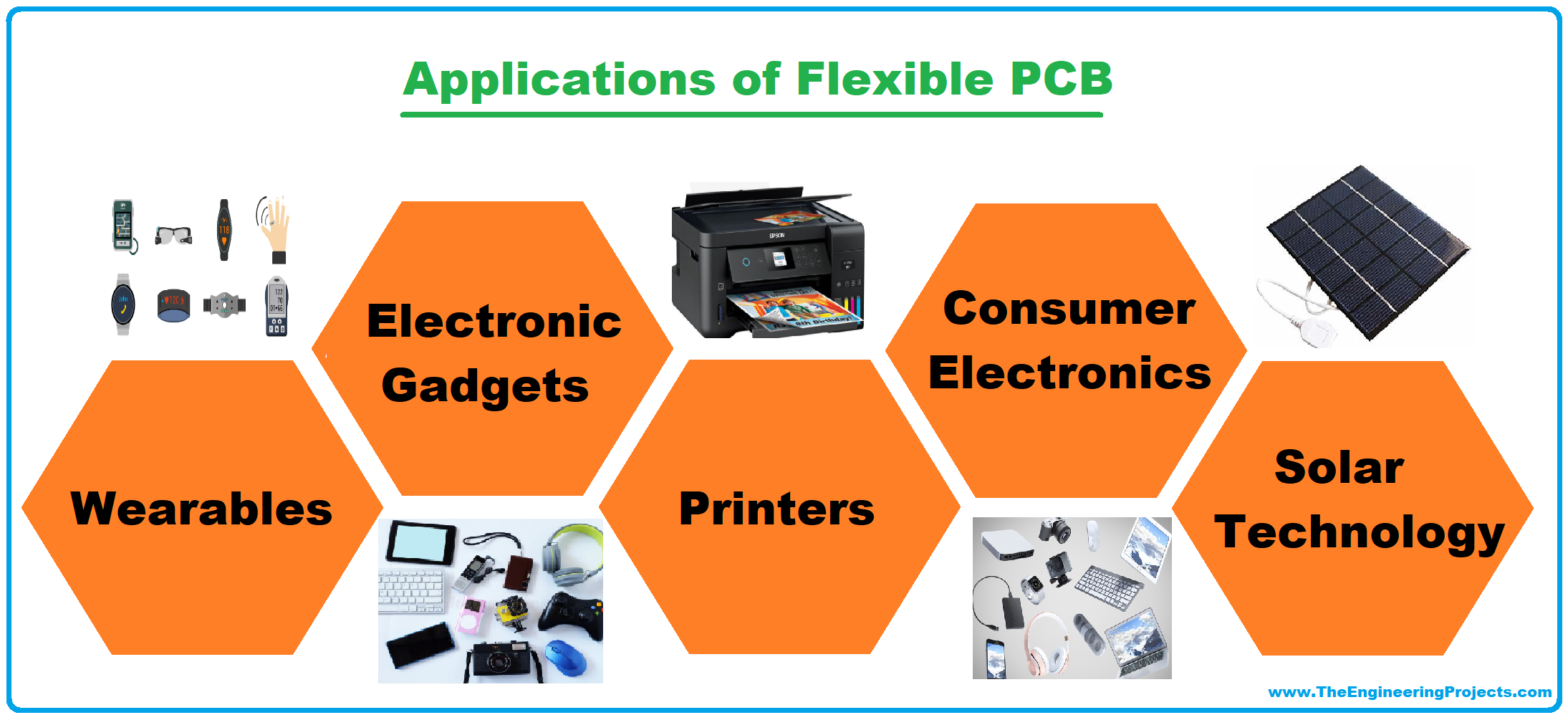
1. Wearables
- Flex PCB is normally used in electronic wearable devices i.e. wristwatches, lockets, spy microphones, smart cameras etc.
2. Electronic Gadgets
- Flexible PCB is also used in electronic gadgets i.e. mobile phones, computer keyboards, CD/DVD drives etc.
3. Connectors
- Connectors, used in expensive electronic products, are normally designed using Flex PCB.
- Flex connectors avoid wiring & connection problems.
4. Printers
- Moving print-head of printers make use of flexible circuits that provide a pathway to connect signal with moving arm of the disk drive.
6. Consumer Electronics
- Many consumer electronics are incorporated with flexible circuits including calculators, cameras, personal entertainment devices and exercise monitors.
7. Solar Technology
- A flexible solar cell is another addition in the field of flexible electronics which are lightweight, can be folded or twisted into any shape, and are mainly used for power satellites.
That's all for today. I hope you have found this article useful. Keep updating us with your feedback and suggestions, they allow us to give you quality work that resonates with your expectations If you have any questions you can ask me in the comment section below. I'd love to help you according to the best of my expertise. Thanks for reading the article. Stay Tuned!